Method for performing durable flame-retardant grafting modification on fabric through cooperation of low-temperature plasma with electron beam irradiation
A low-temperature plasma, electron beam radiation technology, applied in physical treatment, plant fibers, textiles and papermaking, etc., can solve problems such as increasing unsafe factors, achieve simple and easy operation, durable flame retardant effect, and reduce sewage discharge Effect
- Summary
- Abstract
- Description
- Claims
- Application Information
AI Technical Summary
Problems solved by technology
Method used
Examples
Embodiment 1
[0031] First place the linen fabric in the working gas as N 2 , the working pressure is 10Pa, and the discharge power is 100W, the low-temperature plasma device is pretreated for 120s, and then the fabric is pretreated with sodium hydroxide solution at 95-100°C for 30min to remove impurities, and then the fabric is fully washed After removing the residual alkali, put the fabric in an oven for drying at a temperature of 80-90°C. The fabric was removed after drying and the mass of the linen was weighed. Then soak the fabric in the acrylamide monomer solution with a concentration of 2mol / l for 2.5h, and then put the fabric into a high-energy electron beam for irradiation after one-dipping and one-rolling (the speed of the padding car is 1m / min, the pressure is 0.1Mpa). Irradiation dose was 22KGy. After the reaction, the fabric was taken out and cleaned with deionized water to remove homopolymers and unreacted graft monomers on the surface of the fabric, and finally dried in an o...
Embodiment 2
[0033] First place the linen fabric in the working gas as N 2 , the working pressure is 10Pa, the discharge power is 100W in the low-temperature plasma device pretreatment for 150s, and then the fabric is pretreated with sodium hydroxide solution at 95-100°C for 30min to remove impurities, and then the fabric is fully washed After removing the residual alkali, put the fabric in an oven for drying at a temperature of 80-90°C. The fabric was removed after drying and the mass of the linen was weighed. Then soak the fabric in the acrylamide monomer solution with a concentration of 2mol / l for 2.5h, and then put the fabric into a high-energy electron beam for irradiation after one-dipping and one-rolling (the speed of the padding car is 1m / min, the pressure is 0.1Mpa). Irradiation dose was 43KGy. After the reaction, the fabric was taken out and cleaned with deionized water to remove homopolymers and unreacted graft monomers on the surface of the fabric, and finally dried in an oven...
Embodiment 3
[0035] First place the linen fabric in the working gas as N 2, the working pressure is 10Pa, and the discharge power is 100W, the low-temperature plasma device is pretreated for 180s, and then the fabric is pretreated with sodium hydroxide solution for 30min at 95-100°C to remove impurities, and then the fabric is fully washed After removing the residual alkali, put the fabric in an oven for drying at a temperature of 80-90°C. The fabric was removed and the mass of the linen was weighed. Then soak the fabric in the acrylamide monomer solution with a concentration of 2mol / l for 2.5h, and then put the fabric into a high-energy electron beam for irradiation after one-dipping and one-rolling (the speed of the padding car is 1m / min, the pressure is 0.1Mpa). Irradiation dose was 65KGy. After the reaction, the fabric was taken out and cleaned with deionized water to remove homopolymers and unreacted graft monomers on the surface of the fabric, and finally dried in an oven to constan...
PUM
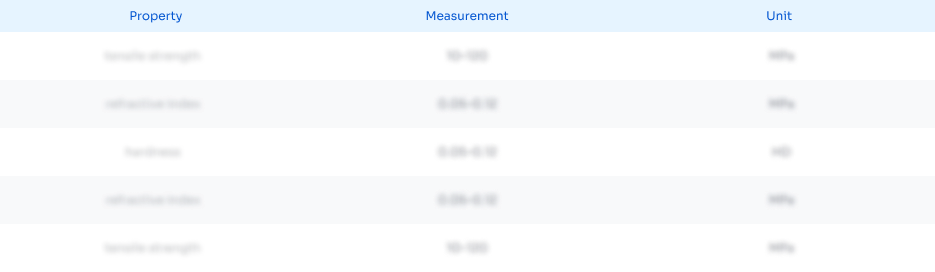
Abstract
Description
Claims
Application Information

- R&D
- Intellectual Property
- Life Sciences
- Materials
- Tech Scout
- Unparalleled Data Quality
- Higher Quality Content
- 60% Fewer Hallucinations
Browse by: Latest US Patents, China's latest patents, Technical Efficacy Thesaurus, Application Domain, Technology Topic, Popular Technical Reports.
© 2025 PatSnap. All rights reserved.Legal|Privacy policy|Modern Slavery Act Transparency Statement|Sitemap|About US| Contact US: help@patsnap.com