Casting residual steel slag recycling method
A technology of steel slag recovery and excess injection, which is applied in the field of iron and steel metallurgy to achieve the effects of accelerating slag flow, reducing the consumption of cold slag materials and reducing the temperature drop.
- Summary
- Abstract
- Description
- Claims
- Application Information
AI Technical Summary
Problems solved by technology
Method used
Image
Examples
Embodiment 1
[0041] Embodiment 1. The slag injection of furnace number P14608455 is hoisted by a crane to the sky over the trolley, and the ladle slag tank is slowly lowered. When the distance between the two tank mouths is 0.8m, the slag injection is slowly poured into the In the semi-steel empty tank on the straddle trolley, the time from the end of casting to the end of slag turning is controlled within 10 minutes, and the weight of the residual slag is 1.7t. The semi-steel tank on the straddle trolley is transported to the vanadium extraction span, and the transportation time is 31 minutes , the semi-steel tank is discharged from the vanadium extracting furnace P14518730, the furnace shakes slowly when the semi-steel is discharged, and the slag liquid foams and rises, add 0.72Kg / t to the semi-steel tank 半钢 Deoxidation of aluminum and iron reduces the consumption of semi-steel covering agent by 0.53Kg / t 半钢 . After the semi-steel is produced, it is transported to the steelmaking convert...
Embodiment 2
[0042] Example 2: Smelting No. P14608723 heat continuous casting slag injection is hoisted by a crane to the sky over the trolley, and the ladle slag tank is slowly lowered. When the distance between the two tank mouths is 0.7m, slowly pour the slag injection into the overpass In the semi-steel empty tank on the straddle trolley, the time from the end of casting to the end of slag turning is controlled at 11 minutes, and the weight of the residual slag is 1.5t. The semi-steel tank on the straddle trolley is transported to the vanadium extraction span, and the transportation time is 35 minutes , the semi-steel tank is discharged from the vanadium extracting furnace P14519393. When the semi-steel is discharged, the furnace shakes slowly, and the slag liquid foams and rises. Add 0.65Kg / t to the semi-steel tank 半钢 Deoxidation of aluminum and iron reduces the consumption of semi-steel covering agent by 0.85Kg / t 半钢 . After the semi-steel is produced, it is transported to the steelm...
PUM
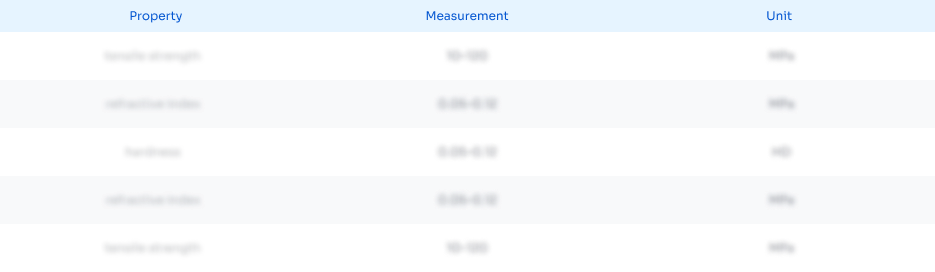
Abstract
Description
Claims
Application Information

- R&D
- Intellectual Property
- Life Sciences
- Materials
- Tech Scout
- Unparalleled Data Quality
- Higher Quality Content
- 60% Fewer Hallucinations
Browse by: Latest US Patents, China's latest patents, Technical Efficacy Thesaurus, Application Domain, Technology Topic, Popular Technical Reports.
© 2025 PatSnap. All rights reserved.Legal|Privacy policy|Modern Slavery Act Transparency Statement|Sitemap|About US| Contact US: help@patsnap.com