Composite reinforced winding-type pressure pipe and forming method thereof
A composite reinforcement and winding technology, which is applied in the field of plastic pressure pipes, can solve the problems of low strength, complex molding process, and instability of plastic reinforced pressure pipes, and achieve better reinforcement effect, simple molding process, and uniform strength.
- Summary
- Abstract
- Description
- Claims
- Application Information
AI Technical Summary
Problems solved by technology
Method used
Image
Examples
Embodiment Construction
[0040] In order to make the technical problems, technical solutions and beneficial effects to be solved by the present invention clearer and clearer, the present invention will be further described in detail below in conjunction with the accompanying drawings and embodiments. It should be understood that the specific embodiments described here are only used to explain the present invention, not to limit the present invention.
[0041] Such as figure 1 as shown, figure 1 It is a schematic cross-sectional view of the composite reinforced wound pressure pipe along the radial direction. In this embodiment, the composite reinforced wound pressure pipe includes a plastic outer layer 10 , a plastic inner layer 30 and a long glass fiber sheet reinforced plastic layer 20 arranged between the plastic outer layer 10 and the plastic inner layer 30 . Wherein, the long-wave fiber sheet reinforced plastic layer 20 includes a long-wave fiber sheet 22 and a plastic composite layer 21 coverin...
PUM
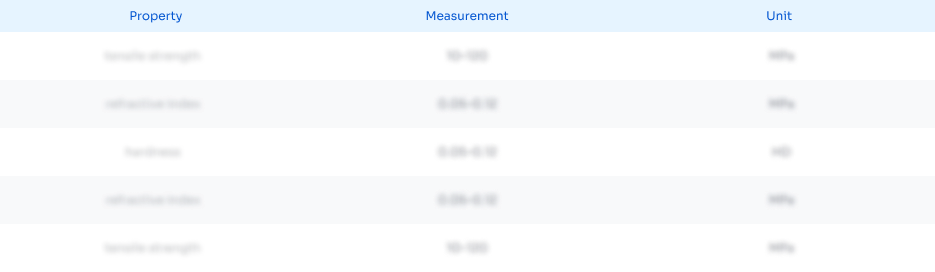
Abstract
Description
Claims
Application Information

- R&D Engineer
- R&D Manager
- IP Professional
- Industry Leading Data Capabilities
- Powerful AI technology
- Patent DNA Extraction
Browse by: Latest US Patents, China's latest patents, Technical Efficacy Thesaurus, Application Domain, Technology Topic, Popular Technical Reports.
© 2024 PatSnap. All rights reserved.Legal|Privacy policy|Modern Slavery Act Transparency Statement|Sitemap|About US| Contact US: help@patsnap.com