Halogen-free epoxy resin flame retardant and preparation method thereof
A halogenated epoxy resin and flame retardant technology, applied in the field of chemical synthesis agent and its preparation, to achieve the effects of high purity, easy control and convenient post-processing
- Summary
- Abstract
- Description
- Claims
- Application Information
AI Technical Summary
Problems solved by technology
Method used
Image
Examples
Embodiment 1
[0025] The first step: to the equipped with reflux condenser, thermometer N 2 Add 13.62g of pentaerythritol and 23.8ml of phosphorus oxychloride into the 250ml three-necked bottle of the introduction tube and magnet, then add 80ml of chlorobenzene as solvent, 0.3g of AlCl 3 as a catalyst. Pass N 2 Protection, the temperature was raised to 60°C to start the reaction, after 1 hour, the temperature was raised to 80°C for 3 hours, and then the temperature was raised to 100°C for 8 hours. Pass N after the reaction 2 Protected and cooled to room temperature, a white liquid was obtained. After the liquid was filtered, washed and dried, a white powdery solid was obtained.
[0026] Step 2: Add 5.94g of SPDPC to a 100ml three-necked flask equipped with magnetic stirring, dropping funnel and thermometer, then add 30ml of DMF as a solvent, add 3.4ml of glycidol and 10ml of DMF solvent in the dropping funnel to dilute, start under ice bath Add dropwise, after 1.5h dropwise addition, na...
Embodiment 2
[0028] The first step: the synthetic method of phosphorus, nitrogen intermediate is the same as embodiment 1.
[0029] Step 2: Add SPDPC11.88g into a 100ml three-necked flask equipped with magnetic stirring, dropping funnel and thermometer, then add 40ml of DMF as a solvent, add 6.8ml of glycidol and 15ml of DMF solvent in the dropping funnel to dilute, start under ice bath Add dropwise, after 2 hours of dropwise addition, naturally warm up to room temperature, react until no HCl gas is released, and end the reaction, after treatment, a milky white liquid can be obtained.
Embodiment 3
[0031] The first step: the synthetic method of phosphorus, nitrogen intermediate is the same as embodiment 1.
[0032] Step 2: Add SPDPC23.76g into a 250ml three-necked bottle equipped with magnetic stirring, dropping funnel and thermometer, then add 100ml of DMF as solvent, add 17ml of glycidol and 25ml of DMF solvent in the dropping funnel to dilute, and start dripping under ice bath Add, after 2 hours of dropwise addition, naturally warm up to room temperature, react until no HCl gas is released, and end the reaction, after treatment, a milky white liquid can be obtained.
PUM
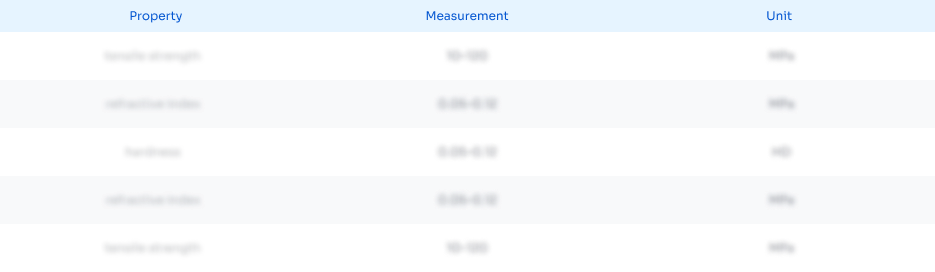
Abstract
Description
Claims
Application Information

- R&D
- Intellectual Property
- Life Sciences
- Materials
- Tech Scout
- Unparalleled Data Quality
- Higher Quality Content
- 60% Fewer Hallucinations
Browse by: Latest US Patents, China's latest patents, Technical Efficacy Thesaurus, Application Domain, Technology Topic, Popular Technical Reports.
© 2025 PatSnap. All rights reserved.Legal|Privacy policy|Modern Slavery Act Transparency Statement|Sitemap|About US| Contact US: help@patsnap.com