Double-freedom degree rotation device driven by ultrasonic motor
An ultrasonic motor and rotating device technology, applied in electromechanical devices, generators/motors, electric components, etc., can solve the problems of low driving accuracy, complex structure, large volume, etc., and achieve small size, compact overall structure, and high precision. Effect
- Summary
- Abstract
- Description
- Claims
- Application Information
AI Technical Summary
Problems solved by technology
Method used
Image
Examples
specific Embodiment approach 1
[0014] Specific implementation mode one: combine Figure 1-Figure 5 Explain that a two-degree-of-freedom rotating device driven by an ultrasonic motor in this embodiment includes a supine motion mechanism and an azimuth motion mechanism;
[0015] The azimuth movement mechanism includes an azimuth ultrasonic motor 4, an azimuth ultrasonic motor seat 5 and an azimuth encoder 8;
[0016] The supine motion mechanism includes a pitching ultrasonic motor 3, a pitching ultrasonic motor seat 6 and a pitching encoder 9;
[0017] The azimuth ultrasonic motor 4 is installed on the azimuth ultrasonic motor base 5, the shaft of the azimuth encoder 8 is coaxially connected to the motor shaft of the azimuth ultrasonic motor 4, and the output shaft of the azimuth ultrasonic motor 4 is connected to the pitch ultrasonic motor base 6;
[0018] The pitching ultrasonic motor 3 is installed on the pitching ultrasonic motor base 6, the shaft of the pitching encoder 9 is coaxially connected with the...
specific Embodiment approach 2
[0020] Specific implementation mode two: combination Figure 1-Figure 5 Note that the azimuth ultrasonic motor 4 in this embodiment is a traveling wave rotary ultrasonic motor or a standing wave rotary ultrasonic motor. Such a setting is small in size, light in weight, convenient and reliable in use, and meets actual needs. The load can rotate 360° around the output shaft of the azimuth ultrasonic motor 4, and the load can rotate ≥ 180° around the output shaft of the pitch ultrasonic motor 3. Others are the same as in the first embodiment.
specific Embodiment approach 3
[0021] Specific implementation mode three: combination Figure 1-Figure 5 Note that the pitching ultrasonic motor 3 of this embodiment is a traveling wave rotary ultrasonic motor or a standing wave rotary ultrasonic motor. Such a setting is small in size, light in weight, convenient and reliable in use, and meets actual needs. The load can rotate 360° around the output shaft of the azimuth ultrasonic motor 4, and the load can rotate ≥ 180° around the output shaft of the pitch ultrasonic motor 3. Others are the same as in the first or second embodiment.
PUM
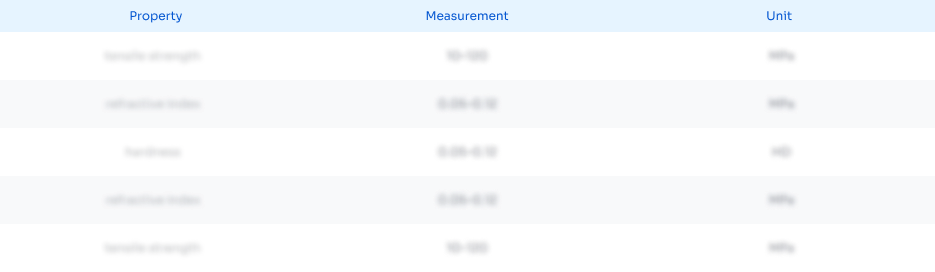
Abstract
Description
Claims
Application Information

- Generate Ideas
- Intellectual Property
- Life Sciences
- Materials
- Tech Scout
- Unparalleled Data Quality
- Higher Quality Content
- 60% Fewer Hallucinations
Browse by: Latest US Patents, China's latest patents, Technical Efficacy Thesaurus, Application Domain, Technology Topic, Popular Technical Reports.
© 2025 PatSnap. All rights reserved.Legal|Privacy policy|Modern Slavery Act Transparency Statement|Sitemap|About US| Contact US: help@patsnap.com