Naphtha-containing water-borne acrylic resin and preparation method thereof
A technology of water-based acrylic acid and naphtha, applied in the field of water-based acrylic resin containing naphtha, can solve the problems of low solid content, poor gloss, high emulsion viscosity and the like
- Summary
- Abstract
- Description
- Claims
- Application Information
AI Technical Summary
Problems solved by technology
Method used
Image
Examples
Embodiment 1
[0129] (1) Add 50.1g of naphtha, 102.93g of ethylene glycol butyl ether, and 3.99g of n-dodecanethiol into a 2000mL four-neck flask equipped with a stirrer, a reflux condenser, and a separatory funnel, and start the stirrer. The control temperature is 80°C;
[0130] (2) Add the mixture A (methyl methacrylate 57.85g, butyl acrylate 52.61g, hydroxyethyl methacrylate 34.62g, vinyltrioxysilane 7.33g, azobisisobutyronitrile) in about 3 hours. 2.99g, filtered after ultrasonic dispersion);
[0131] (3) Add 0.6 g of azobisisobutyronitrile, 0.6 g of n-dodecylmercaptan, and 20.21 g of ethylene glycol butyl ether (directly added after ultrasonic dispersion) to the system obtained in step 2, and insulate and react for 1 h at 80°C ,
[0132] (4) Add dropwise mixture B (86.85g of methyl methacrylate, 12.06g of methacrylic acid, 80.34g of butyl acrylate, 52.09g of hydroxyethyl methacrylate, vinyl trioxysilane) to the system obtained in step 3 11.62g, 5.02g of azobisisobutyronitrile, filte...
Embodiment 2
[0137] (1) Add 80g of naphtha, 100g of ethylene glycol butyl ether, and 6g of octadecyl mercaptan in a 2000mL four-necked flask equipped with an agitator, a reflux condenser and a separatory funnel, and start the agitator to control the temperature of the water bath. 85°C;
[0138] (2) Add the mixture A (methyl methacrylate 80g, butyl acrylate 70g, hydroxyethyl methacrylate 40g, vinyltrioxysilane 6g, azobisisobutyronitrile 5g, ultrasonically disperse postfilter);
[0139] (3) Add 0.3 g of azobisisobutyronitrile, 0.8 g of n-octadecyl mercaptan, and 10 g of ethylene glycol butyl ether (directly added after ultrasonic dispersion) to the system obtained in step 2, and insulate and react at 85° C. for 1 h,
[0140] (4) Add dropwise mixture B (methyl methacrylate 100g, methacrylic acid 15g, butyl acrylate 60g, hydroxyethyl methacrylate 70g, vinyltrioxysilane 8g, azo Diisobutyronitrile 8g, filtered after ultrasonic dispersion), dripped in about 2 hours,
[0141] (5) Add 0.5 g of azo...
Embodiment 3
[0145] (1) Add 20g of naphtha, 100g of ethylene glycol butyl ether, and 3g of n-dodecanethiol in a 2000mL four-neck flask equipped with an agitator, a reflux condenser and a separatory funnel, and start the agitator to control the temperature of the water bath. 90°C;
[0146] (2) Add the mixture A (methyl methacrylate 70g, butyl acrylate 80g, hydroxyethyl methacrylate 30g, vinyltrioxysilane 9g, azobisisobutyronitrile 1g) in about 5 hours, and ultrasonically disperse postfilter);
[0147] (3) Add 0.8 g of azobisisobutyronitrile, 0.4 g of n-dodecanethiol, and 30 g of ethylene glycol butyl ether (directly added after ultrasonic dispersion) to the system obtained in step 2, and insulate and react for 1 h at 90° C.,
[0148] (4) Add dropwise mixture B (methyl methacrylate 60g, methacrylic acid 8g, butyl acrylate 100g, hydroxyethyl methacrylate 30g, vinyltrioxysilane 15g, azo Diisobutyronitrile 3g, filtered after ultrasonic dispersion), dripped in about 5h,
[0149] (5) Add 2 g o...
PUM
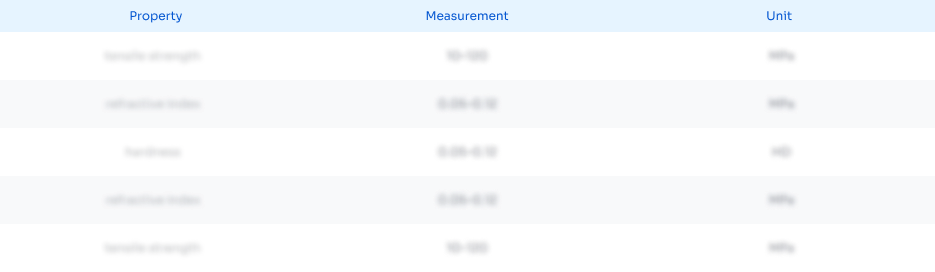
Abstract
Description
Claims
Application Information

- Generate Ideas
- Intellectual Property
- Life Sciences
- Materials
- Tech Scout
- Unparalleled Data Quality
- Higher Quality Content
- 60% Fewer Hallucinations
Browse by: Latest US Patents, China's latest patents, Technical Efficacy Thesaurus, Application Domain, Technology Topic, Popular Technical Reports.
© 2025 PatSnap. All rights reserved.Legal|Privacy policy|Modern Slavery Act Transparency Statement|Sitemap|About US| Contact US: help@patsnap.com