Preparation method for smelting electrodes
An electrode and a technology for preparing electrodes, which are applied in the field of alloy ingot manufacturing, can solve problems such as wide distribution, leakage of molten tumors, electrode oxidation, etc., and achieve the effects of simple preparation steps, wide application range, and good use effect
- Summary
- Abstract
- Description
- Claims
- Application Information
AI Technical Summary
Problems solved by technology
Method used
Examples
Embodiment 1
[0022] Example 1: An electron beam furnace was used to smelt an ingot of industrial pure titanium TA2 with a specification of Φ720 mm.
[0023] Step 1: Use pure titanium tubes and strips of pure titanium plates that pass the surface inspection after treatment and whose quality meets the requirements, and distinguish them by length;
[0024] Step 2. According to the principle that longer length raw materials are placed on the periphery and shorter length raw materials are placed inside, the differentiated raw materials are placed in a Φ600mm forming mold to form the raw materials into columnar raw materials;
[0025] Step 3: After fastening the columnar raw materials with a fastening device, use TA2 grade pure titanium strips with a width of 3mm and a thickness of 0.5mm to bundle them at intervals of 300mm along the longitudinal direction to shape them into electrodes for smelting.
[0026] Step 4: Melting into a Φ720mm finished ingot in an electron beam furnace, main process p...
Embodiment 2
[0028] Example 2: An industrial titanium alloy TA18 ingot with a specification of Φ820 mm was smelted in a vacuum consumable electric arc furnace.
[0029] Step 1: Use TC4 and TA2 grades of titanium alloy plates, rods and tubular materials that have passed the surface inspection after treatment and whose quality meets the requirements, and distinguish them by length and grade. According to the composition control requirements of TA18 titanium alloy, use TC4 and TA2 grades The strip raw materials are batched according to the weight ratio of 1:1, and the amount of TA2 brand pure titanium strips for subsequent bundling is reserved. At the same time, a certain amount of pure aluminum plates are added to supplement the aluminum content in the electrode to the target batching composition.
[0030] Step 2. According to the principle that longer length raw materials are placed on the periphery and shorter length raw materials are placed inside, the differentiated raw materials are plac...
Embodiment 3
[0034] Example 3: Melting an ingot of industrial titanium alloy TC4 with a specification of Φ220 mm in a shell furnace.
[0035] Step 1: Use titanium alloy TC4 brand rod-shaped materials and strip-shaped plate materials that pass the surface inspection after treatment and whose quality meets the requirements, and distinguish them by length;
[0036] Step 2. According to the principle that longer length raw materials are placed on the periphery and shorter length raw materials are placed inside, the differentiated raw materials are placed in a forming mold with a diameter of Φ200mm, so that the raw materials are formed into columnar raw materials;
[0037] Step 3: After fastening the columnar raw materials with a fastening device, use TA2 grade pure titanium strips with a width of 3mm and a thickness of 0.5mm to bundle them at intervals of 200mm along the longitudinal direction to shape them into electrodes for smelting.
[0038] Step 4: Melting in a shell furnace into Φ220mm i...
PUM
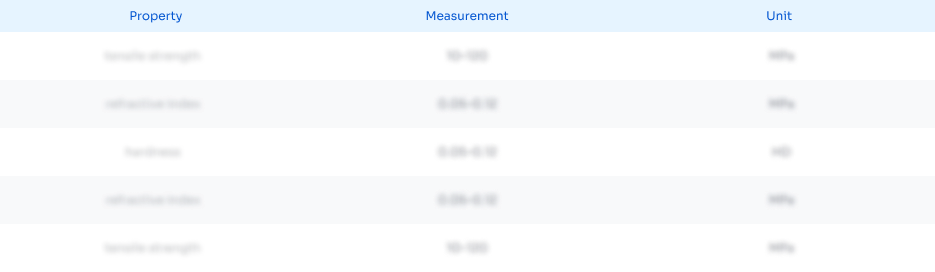
Abstract
Description
Claims
Application Information

- R&D Engineer
- R&D Manager
- IP Professional
- Industry Leading Data Capabilities
- Powerful AI technology
- Patent DNA Extraction
Browse by: Latest US Patents, China's latest patents, Technical Efficacy Thesaurus, Application Domain, Technology Topic, Popular Technical Reports.
© 2024 PatSnap. All rights reserved.Legal|Privacy policy|Modern Slavery Act Transparency Statement|Sitemap|About US| Contact US: help@patsnap.com