Isoalkane/olefin alkylation method and device
An isoparaffin and alkylation technology, applied in the field of alkylation of isoparaffins and olefins, can solve the problems of large difference in reaction conditions, high energy consumption of process systems, low life and other problems, and achieve volume reduction, area/area reduction, etc. The effect of increasing volume ratio, enhancing mass transfer and heat transfer
- Summary
- Abstract
- Description
- Claims
- Application Information
AI Technical Summary
Problems solved by technology
Method used
Image
Examples
Embodiment 1
[0075] The alkylation method of isoparaffins and olefins, the steps are as follows:
[0076] The catalyst composed of isoparaffin and solid Y-type molecular sieve is mixed and passed into the microreactor, and olefin is passed into it at the same time. The alkene ratio of isoparaffin and olefin is 3:1, and the reaction space velocity is 1.1h -1 ;
[0077] The particles of the solid Y-type molecular sieve catalyst are less than 20 μm, and form a suspension slurry with a solid content of less than 25% in the alkane solution;
[0078] The reaction conditions of the control microreactor are: reaction temperature 100°C, reaction pressure 1.5MPa;
[0079] The product after the reaction is separated to obtain the target reaction product, unreacted reactant and catalyst respectively;
[0080] The unreacted reactants are directly passed into the microreactor to continue the reaction;
[0081] After supercritical extraction, the catalyst is re-mixed with isoparaffin, and then passed in...
Embodiment 2
[0086] The alkylation method of isoparaffins and olefins, the steps are as follows:
[0087] The isoparaffin is mixed with the solid superacid catalyst and passed into the microreactor, and the olefin is simultaneously passed into it. The alkene ratio of the isoparaffin and the olefin is 10:1, and the reaction space velocity is 1.2h -1 ;
[0088] The particles of the solid acid alkylation catalyst are less than 20 μm, and form a suspension slurry with a solid content of 20% in the alkane solution;
[0089] The reaction conditions of the control microreactor are: reaction temperature 40°C, reaction pressure 4.5MPa;
[0090] The product after the reaction is separated to obtain the target reaction product, unreacted reactant and catalyst respectively;
[0091] The unreacted reactants are directly passed into the microreactor to continue the reaction;
[0092] After supercritical extraction, the catalyst is re-mixed with isoparaffin, and then passed into the microreactor for r...
Embodiment 3
[0097] The alkylation method of isoparaffins and olefins, the steps are as follows:
[0098] The isoparaffin is mixed with the solid superacid catalyst and passed into the microreactor, and the olefin is simultaneously passed into it. The alkene ratio of the isoparaffin and the olefin is 50:1, and the reaction space velocity is 1.3h -1 ;
[0099] The particles of the solid acid alkylation catalyst are less than 20 μm, and form a suspension slurry with a solid content of 15% in the alkane solution;
[0100] The reaction conditions of the control microreactor are: reaction temperature 200°C, reaction pressure 1.5MPa;
[0101] The product after the reaction is separated to obtain the target reaction product, unreacted reactant and catalyst respectively;
[0102] The unreacted reactants are directly passed into the microreactor to continue the reaction;
[0103] After the catalyst is supercritically extracted, it is re-introduced into the microreactor for reaction;
[0104] Am...
PUM
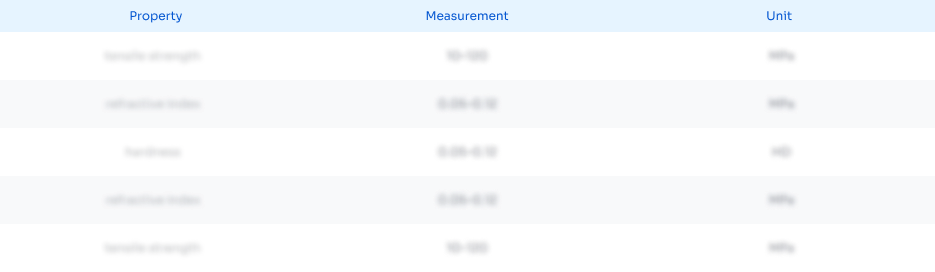
Abstract
Description
Claims
Application Information

- R&D
- Intellectual Property
- Life Sciences
- Materials
- Tech Scout
- Unparalleled Data Quality
- Higher Quality Content
- 60% Fewer Hallucinations
Browse by: Latest US Patents, China's latest patents, Technical Efficacy Thesaurus, Application Domain, Technology Topic, Popular Technical Reports.
© 2025 PatSnap. All rights reserved.Legal|Privacy policy|Modern Slavery Act Transparency Statement|Sitemap|About US| Contact US: help@patsnap.com