An er/sc/zr composite micro-alloyed al-6mg-0.4mn alloy stabilization annealing process
A stabilization annealing and micro-alloying technology, applied in the field of heat treatment technology, can solve the problems that the mechanical properties and corrosion properties of the alloy cannot be satisfied at the same time, stabilization difficulties, intergranular corrosion, etc., to achieve good long-term intergranular corrosion resistance, widening Temperature range, the effect of improving the service life
- Summary
- Abstract
- Description
- Claims
- Application Information
AI Technical Summary
Problems solved by technology
Method used
Image
Examples
Embodiment 1
[0019] 1) Taking Er / Sc / Zr composite microalloyed Al-Mg-Mn alloy as an example, the chemical composition is Mg5.5%~6.5%, Mn0.4%~0.5%, Zr0.1%~0.15%, Er0% ~0.09%, Sc0.04%~0.1% Unavoidable impurity content <0.4%, the alloy is homogenized annealed at 300°C (7-12h) + 475°C (15h), hot rolled at 450°C for 2h, hot rolled deformation The amount is about 70%, cold rolling after intermediate annealing at 475°C / 5h, and the final cold deformation amount is 60%±2%.
[0020] 2) The cold-rolled sheet obtained in step 1) was annealed at 240° C. for different times, and air-cooled to room temperature. According to the American Society for Testing and Materials standard AST G67, the nitric acid weight loss test was carried out on the cold-rolled and different annealed samples of the alloy, and the intergranular corrosion susceptibility of the material was evaluated by the weight loss per unit area of the alloy before and after immersion. The change curve of weight loss per unit area with annea...
Embodiment 2
[0022] Step 1) is the same as in Example 1.
[0023] 2) The cold-rolled sheet obtained in step 1) was annealed at 265° C. for different times, and air-cooled to room temperature. According to the American Society for Testing and Materials standard AST G67, the nitric acid weight loss test was carried out on the cold-rolled and different annealed samples of the alloy, and the intergranular corrosion susceptibility of the material was evaluated by the weight loss per unit area of the alloy before and after immersion. The change curve of weight loss per unit area with annealing time is as follows: figure 2 shown.
Embodiment 3
[0030] Step 1) Taking Er / Sc / Zr composite microalloyed Al-Mg-Mn alloy as an example, the chemical composition is Mg5.5%~6.5%, Mn0.4%~0.5%, Zr0.1%~0.15%, Er0 .09%, Sc0.1% unavoidable impurity content <0.4%, the alloy is homogenized annealed at 300°C (7-12h)+475°C (15h), hot rolled at 450°C for 2h, and the hot rolling deformation is about 70%, cold rolling after intermediate annealing at 475°C / 5h, until the final cold deformation is 60%±2%.
[0031] 2) After annealing the cold-rolled sheet obtained in step 1) at 240° C. for different times (10, 24 h), air-cool to room temperature.
[0032] 3) The annealed samples obtained in step 2) were annealed at 150° C. for different times. According to the American Society for Testing and Materials standard AST G67, the nitric acid weight loss test was carried out on the alloy samples in different annealed states, and the intergranular corrosion susceptibility of the material was evaluated by the weight loss per unit area of the alloy bef...
PUM
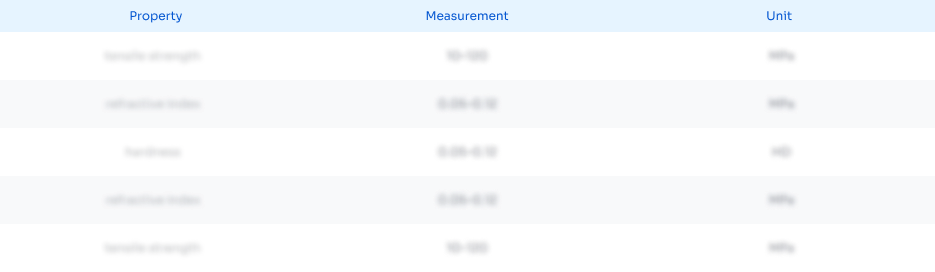
Abstract
Description
Claims
Application Information

- R&D Engineer
- R&D Manager
- IP Professional
- Industry Leading Data Capabilities
- Powerful AI technology
- Patent DNA Extraction
Browse by: Latest US Patents, China's latest patents, Technical Efficacy Thesaurus, Application Domain, Technology Topic, Popular Technical Reports.
© 2024 PatSnap. All rights reserved.Legal|Privacy policy|Modern Slavery Act Transparency Statement|Sitemap|About US| Contact US: help@patsnap.com