Preparation method for citraconic anhydride
A technology of citraconic anhydride and itaconic acid, applied in the direction of organic chemistry, can solve the problems of harsh reaction conditions, high reaction temperature, and many by-products, and achieve the effects of convenient solvent recovery, simple post-treatment, and no impact on yield
- Summary
- Abstract
- Description
- Claims
- Application Information
AI Technical Summary
Problems solved by technology
Method used
Examples
Embodiment 1
[0015] Example 1: 0.10g of strontium sulfate, 10.0g of itaconic acid and 10.0g of tetrahydronaphthalene were added to a reactor equipped with an oil-water separator, a thermometer and agitation, and the reaction was stopped after water separation at 210°C for 4 hours, and the resulting product was decompressed Distillation, under a vacuum of 300Pa, distill the solvent at 85°C to recover the solvent, and collect the product at 100°C to obtain a colorless liquid product, citraconic anhydride, with a yield of 99.0% and a purity of 99.6%.
Embodiment 2
[0019] Embodiment 2: 0.10g magnesium sulfate, 50.0g itaconic acid and 500.0g o-dichlorobenzene are added in the reactor that is equipped with oil-water separator, thermometer and stirring, stop reaction after 10h of water separation reaction at 155 ℃, the gained product is reduced Pressure distillation, under vacuum degree of 300Pa, distill and recover the solvent at 85°C, and collect the product at 100°C to obtain a colorless liquid product, citraconic anhydride, with a yield of 98.2% and a purity of 99.3%.
Embodiment 3
[0020] Example 3: 1.0g of barium sulfate, 50.0g of itaconic acid and 10.0g of xylene were added to a reactor equipped with an oil-water separator, a thermometer and agitation, and the reaction was stopped after 1.0h of water separation at 130°C, and the resulting product was decompressed Distillation, under a vacuum of 300Pa, distill the solvent at 85°C to recover the solvent, and collect the product at 100°C to obtain a colorless liquid product, citraconic anhydride, with a yield of 97.5% and a purity of 99.5%.
PUM
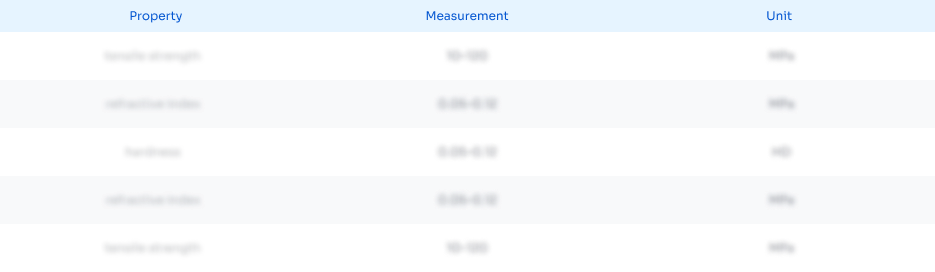
Abstract
Description
Claims
Application Information

- R&D
- Intellectual Property
- Life Sciences
- Materials
- Tech Scout
- Unparalleled Data Quality
- Higher Quality Content
- 60% Fewer Hallucinations
Browse by: Latest US Patents, China's latest patents, Technical Efficacy Thesaurus, Application Domain, Technology Topic, Popular Technical Reports.
© 2025 PatSnap. All rights reserved.Legal|Privacy policy|Modern Slavery Act Transparency Statement|Sitemap|About US| Contact US: help@patsnap.com