Preparation method of compound tungsten-base tubular welding rod hard-face material
A tubular electrode, composite tungsten technology, applied in welding/cutting medium/material, welding equipment, welding medium, etc., can solve the problems of wear resistance, fracture of hard surface layer, tool waste, etc., to achieve high wear resistance Effect
- Summary
- Abstract
- Description
- Claims
- Application Information
AI Technical Summary
Problems solved by technology
Method used
Image
Examples
example 1
[0026] A. Mix raw materials: (1) 50 parts, (2) 10 parts, (3) 30 parts, (4) 6 parts, (5) 1 part, (6) 2.5 parts in a mixer for 2 hours to obtain a mixture .
[0027] B. After unloading the obtained mixture, add 0.5 part of raw material (7) and stir evenly (mix phenolic resin with absolute alcohol, dissolve it at 60°C and pour it into the mixture) and dry it in a drying oven, keep it at 100°C After 3 hours, the temperature was raised to 150° C. for 3 hours, and the finished tubular welding rod hard facing material was obtained after leaving the box.
example 2
[0029] Raw materials: (1) 60 parts, (2) 12 parts, (3) 14 parts, (4) 8 parts, (5) 1.5 parts, (6) 4 parts, and the rest are the same as Example 1.
example 3
[0031] Raw materials: (1) 62 parts, (2) 11 parts, (3) 10 parts, (4) 7 parts, (5) 2 parts, (6) 4.5 parts, and the rest are the same as Example 1.
[0032] The chemical composition of the silicon nitride ceramic particles is Si3N4, which is commercially available.
[0033] The cemented carbide ball particles are self-made by the applicant, and its chemical composition is 94% (wt%) of tungsten carbide (WC) and 6% of Co.
[0034] Spherical tungsten carbide, cast granular tungsten carbide and single grain tungsten carbide are all produced by Zigong Great Wall Hard Surface Material Co., Ltd. and are available in the market.
[0035] The manufacturer of silicon-manganese powder is Shanghai Jiuding Powder Material Co., Ltd., which is commercially available.
[0036] The manufacturer of phenolic resin is Bengbu Tianyu High Temperature Resin Material Co., Ltd., which is commercially available.
[0037] The mixing system is dry mixing, and the mixing machine is made by the applicant.
PUM
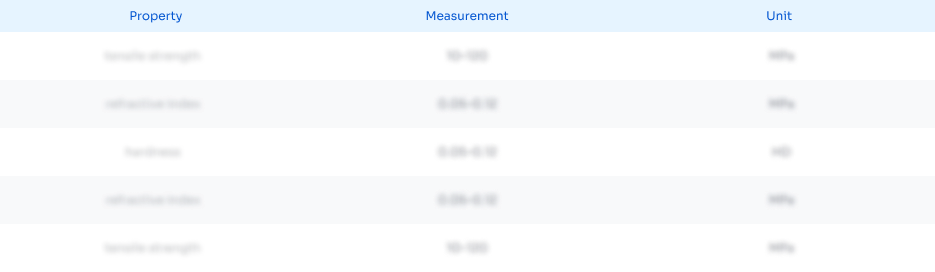
Abstract
Description
Claims
Application Information

- R&D Engineer
- R&D Manager
- IP Professional
- Industry Leading Data Capabilities
- Powerful AI technology
- Patent DNA Extraction
Browse by: Latest US Patents, China's latest patents, Technical Efficacy Thesaurus, Application Domain, Technology Topic, Popular Technical Reports.
© 2024 PatSnap. All rights reserved.Legal|Privacy policy|Modern Slavery Act Transparency Statement|Sitemap|About US| Contact US: help@patsnap.com