Method for removing organic matter in zinc hydrometallurgy raffinate
A technology for hydrometallurgy zinc and raffinate, applied in the field of hydrometallurgy, can solve the problems of inability to completely decompose or completely remove organic substances, ineffective removal, zinc electroplating hazards, etc., and achieve complete removal of organic substances and simple operation. , Efficient removal effect
- Summary
- Abstract
- Description
- Claims
- Application Information
AI Technical Summary
Problems solved by technology
Method used
Examples
Embodiment 1
[0022] The method for removing organic matter from the zinc wet smelting raffinate, its specific steps are as follows: first, 40L of the zinc wet smelting raffinate (after air flotation and active carbon adsorption, P204 content is 35ppm, ethyl xanthate content is 10ppm , fatty acid is 5ppm, Fe 3+ 0.2g / L, Fe 2+ 15g / L, Zn76g / L) into the reactor, adding ferric sulfate to the zinc hydrometallurgy raffinate to make Fe 3+ The concentration is 5g / L~8g / L, and then the temperature of the reactor is controlled at 160°C, and the oxygen partial pressure is maintained at 0.8MPa to react for 4 hours, and then the wet zinc smelting raffinate with organic matter removed can be obtained. After the reaction, the content of P204 in the zinc hydrometallurgy raffinate is 4.0ppm, the content of ethyl xanthate is 0.5ppm, and the fatty acid is less than 0.5ppm.
Embodiment 2
[0024] The method for removing organic matter from the zinc wet smelting raffinate, its specific steps are as follows: first 40L of the zinc wet smelting raffinate (after air flotation P204 content is 60ppm, ethyl xanthate content is 15ppm, Fe 3+ 0.1g / L, Fe 2+ 6g / L, Zn16.5g / L) into the reactor, adding ferric sulfate to the zinc hydrometallurgy raffinate to make Fe 3+ The concentration is 1g / L~3g / L, and then the temperature of the reactor is controlled at 185°C, and the oxygen partial pressure is maintained at 0.15MPa to react for 4 hours, and then the wet zinc smelting raffinate with organic matter removed can be obtained. After the reaction, the P204 content in the zinc hydrometallurgy raffinate was 3.0 ppm, and the ethyl xanthate content was 1.2 ppm.
Embodiment 3
[0026] The method for removing organic matter from the wet zinc smelting raffinate, its specific steps are as follows: first, 40L of the wet zinc smelting raffinate (after air flotation P204 content is 37ppm, hydroxamic acid content is 25ppm, Fe 3+ 0.08g / L, Fe 2+ 12.7g / L, Zn65.9g / L) into the reactor, adding ferric sulfate to the zinc hydrometallurgy raffinate to make Fe 3+ The concentration is 3g / L~6g / L, and then the temperature of the reactor is controlled at 205°C, and the oxygen partial pressure is maintained at 0.4MPa to react for 3 hours, and then the wet zinc smelting raffinate with organic matter removed can be obtained. After the reaction, the content of P204 in the zinc hydrometallurgy raffinate is 4.0ppm, and the hydroxamic acid is less than 1ppm.
PUM
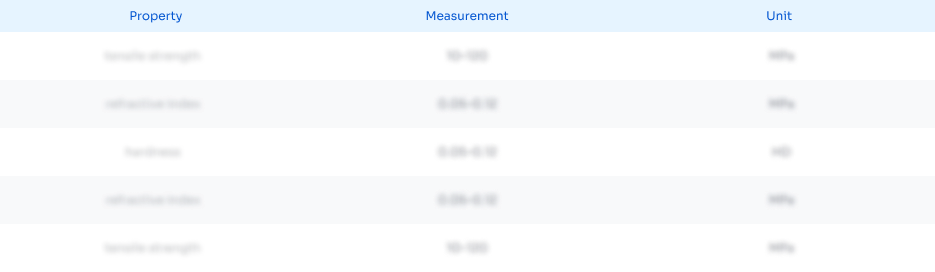
Abstract
Description
Claims
Application Information

- R&D Engineer
- R&D Manager
- IP Professional
- Industry Leading Data Capabilities
- Powerful AI technology
- Patent DNA Extraction
Browse by: Latest US Patents, China's latest patents, Technical Efficacy Thesaurus, Application Domain, Technology Topic, Popular Technical Reports.
© 2024 PatSnap. All rights reserved.Legal|Privacy policy|Modern Slavery Act Transparency Statement|Sitemap|About US| Contact US: help@patsnap.com