Manufacturing method of aluminum alloy for railway vehicle body
A rail vehicle and aluminum alloy technology, which is applied in the field of aluminum alloy material processing, can solve problems such as low yield, feathery crystals, and ingot segregation, and achieve the effects of excellent performance, fine structure, and dense ingot structure
- Summary
- Abstract
- Description
- Claims
- Application Information
AI Technical Summary
Problems solved by technology
Method used
Image
Examples
Embodiment Construction
[0019] The principles and features of the present invention are described below in conjunction with the accompanying drawings, and the examples given are only used to explain the present invention, and are not intended to limit the scope of the present invention.
[0020] A method for preparing an aluminum alloy for a rail vehicle body of the present invention comprises the following steps:
[0021] Step 1) Furnace cleaning and smelting: firstly clean the smelting furnace to clean the inside of the smelting furnace. The leftovers produced when cutting aluminum alloy products with the same composition as aluminum alloy products) are clean and dry, first put small pieces or thin pieces of waste into the smelting furnace, and then add large pieces of waste such as rod heads, and weigh the purity to be more than 99.7% The aluminum ingots are placed on the top of the scrap;
[0022] When the smelting temperature reaches 705°C-720°C, sprinkle 10kg-15kg of slagging agent, close the ...
PUM
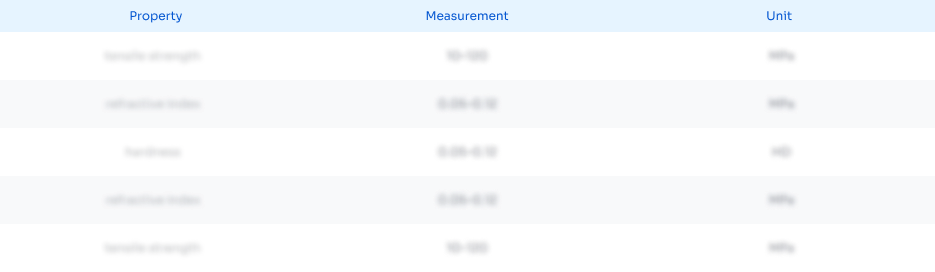
Abstract
Description
Claims
Application Information

- R&D
- Intellectual Property
- Life Sciences
- Materials
- Tech Scout
- Unparalleled Data Quality
- Higher Quality Content
- 60% Fewer Hallucinations
Browse by: Latest US Patents, China's latest patents, Technical Efficacy Thesaurus, Application Domain, Technology Topic, Popular Technical Reports.
© 2025 PatSnap. All rights reserved.Legal|Privacy policy|Modern Slavery Act Transparency Statement|Sitemap|About US| Contact US: help@patsnap.com