Preparation method of damping material used for installing draught fan
A vibration-damping material and a technology for installation, which is applied in the field of vibration-damping materials, can solve the problems of increasing the thickness of the vibration-damping material, complicating the vibration-damping structure, and heavy quality of the vibration-damping material, achieving the effects of enhanced damping, vibration and noise reduction Visible, long-lasting vibration damping effect
- Summary
- Abstract
- Description
- Claims
- Application Information
AI Technical Summary
Problems solved by technology
Method used
Examples
Embodiment 1
[0018] A vibration damping material for fan installation, the vibration damping material is made of the following raw materials in parts by weight: phenolic resin 52, expanded vermiculite 20, polystyrene foam 6, 3-phenyl-2-propyl acrylate 4. Nano carbon black 1, bornyl acetate 8, 2-hydroxyethyl cellulose 2, oxadiazolone 0.2, cristobalite 2, silica sol with a solid content of 10% 2, 100-200 mesh bentonite 20 10, 10 aqueous polyurethane emulsions with a solid content of 8-10%, 10 collagen fibers; 20 waste felts; 2 additives;
[0019] The expanded vermiculite is a particulate matter with numerous small thin-layer pores inside, which is formed by crushing the vermiculite and sintering at a high temperature of 1000-1200 ° C to expand its volume by 15-25 times;
[0020] The collagen fiber is prepared by refining the pretreated waste leather material in a refiner according to a certain concentration;
[0021] The auxiliary agent is made of the following raw materials in parts by wei...
Embodiment 2
[0030] A damping material for fan installation, characterized in that: the damping material is made of the following raw materials in parts by weight: phenolic resin 62, expanded vermiculite 25, polystyrene foam 8, 3-phenyl-2 -Propyl acrylate 6, nano-carbon black 1.5, bornyl acetate 16, 2-hydroxyethyl cellulose 5, oxadiazolone 0.6, cristobalite 5, silica sol with a solid content of 10-15% 3, 100-200 mesh bentonite 24, water-based polyurethane emulsion with a solid content of 8-10% 12, collagen fiber 20; waste felt 30; auxiliary agent 5;
[0031] The expanded vermiculite is a particulate matter with numerous small thin-layer pores inside, which is formed by crushing the vermiculite and sintering at a high temperature of 1000-1200 ° C to expand its volume by 15-25 times;
[0032] The collagen fiber is prepared by refining the pretreated waste leather material in a refiner according to a certain concentration;
[0033] The auxiliary agent is made of the following raw materials i...
PUM
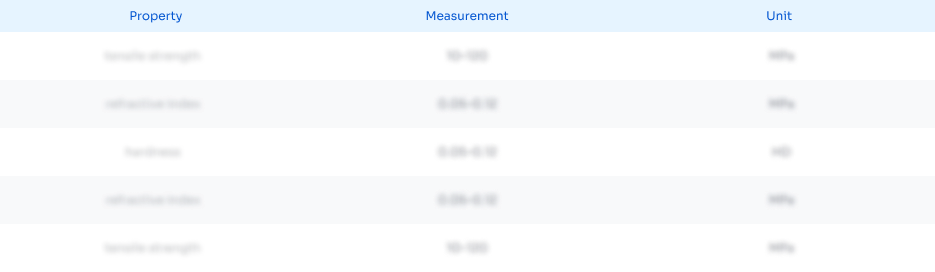
Abstract
Description
Claims
Application Information

- Generate Ideas
- Intellectual Property
- Life Sciences
- Materials
- Tech Scout
- Unparalleled Data Quality
- Higher Quality Content
- 60% Fewer Hallucinations
Browse by: Latest US Patents, China's latest patents, Technical Efficacy Thesaurus, Application Domain, Technology Topic, Popular Technical Reports.
© 2025 PatSnap. All rights reserved.Legal|Privacy policy|Modern Slavery Act Transparency Statement|Sitemap|About US| Contact US: help@patsnap.com