Method for efficiently producing chlorinated graphene
A technology of chlorinated graphene and graphene powder, applied in the field of high-efficiency production of chlorinated graphene, can solve the problems of less research on chlorine-doped graphene, complicated operation, limited application, etc. Good repeatability and uniform chlorine doping effect
- Summary
- Abstract
- Description
- Claims
- Application Information
AI Technical Summary
Problems solved by technology
Method used
Examples
Embodiment 1
[0015] Example 1: Weigh 100g of graphene powder and put it into a chlorination reaction kettle. After the reaction kettle is locked and sealed, the graphene powder is heated. The heating temperature is set at 60°C, and the stirring device is turned on to stir the graphene powder. , so that the graphene powder fills the entire reactor, close the exhaust valve of the reactor (the valve is connected to the chlorine gas recovery device), open the vacuum valve, and vacuumize the reactor. The vacuum pressure is 0.1MPa, and the heating and vacuuming time is 30min. After the moisture in the graphene powder is completely drawn out, close the vacuum valve, stop vacuuming, and heat the graphene powder again. When the temperature reaches 300°C, open the exhaust valve, open the chlorine gas inlet valve, and let in chlorine gas. The flow rate is 450~550 mL / min, and the reaction time is 4~8h. After the reaction, close the chlorine inlet valve, close the chlorine recovery valve, feed nitrogen ...
Embodiment 2
[0016] Example 2: Weigh 100g of graphene powder and put it into the chlorination reaction kettle. After the reaction kettle is locked and sealed, the graphene powder is heated. The heating temperature is set at 60°C, and the stirring device is turned on to stir the graphene powder. , so that the graphene powder fills the entire reactor, close the exhaust valve of the reactor (the valve is connected to the chlorine gas recovery device), open the vacuum valve, and vacuumize the reactor. The vacuum pressure is 0.1MPa, and the heating and vacuuming time is 30min. After the moisture in the graphene powder is completely drawn out, close the vacuum valve, stop vacuuming, and heat up the graphene powder again. When the temperature reaches 450 °C, open the exhaust valve, open the chlorine gas valve, and let in chlorine gas. The flow rate is 450~550 mL / min, and the reaction time is 3~5h. After the reaction, close the chlorine inlet valve, close the chlorine recovery valve, feed nitrogen ...
Embodiment 3
[0017] Example 3: Weigh 100g of graphene powder and put it into the chlorination reaction kettle. After the reaction kettle is locked and sealed, the graphene powder is heated. The heating temperature is set at 60°C, and the stirring device is turned on to stir the graphene powder. , so that the graphene powder fills the entire reactor, close the exhaust valve of the reactor (the valve is connected to the chlorine gas recovery device), open the vacuum valve, and vacuumize the reactor. The vacuum pressure is 0.1MPa, and the heating and vacuuming time is 30min. After the moisture in the graphene powder is completely drawn out, close the vacuum valve, stop vacuuming, and heat the graphene powder again. When the temperature reaches 600°C, open the exhaust valve, open the chlorine gas inlet valve, and let in chlorine gas. The flow rate is 450~550 mL / min, and the reaction time is 1~3h. After the reaction, close the chlorine inlet valve, close the chlorine recovery valve, feed nitroge...
PUM
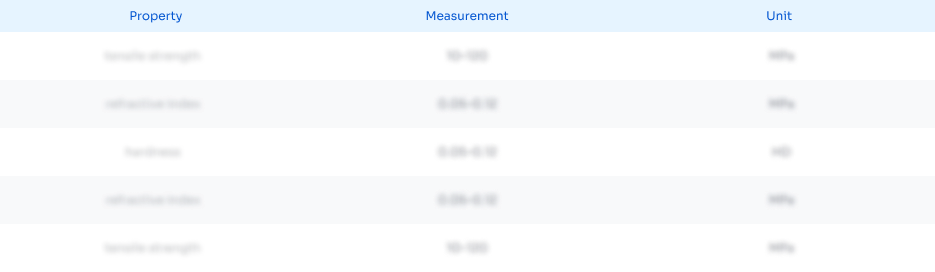
Abstract
Description
Claims
Application Information

- Generate Ideas
- Intellectual Property
- Life Sciences
- Materials
- Tech Scout
- Unparalleled Data Quality
- Higher Quality Content
- 60% Fewer Hallucinations
Browse by: Latest US Patents, China's latest patents, Technical Efficacy Thesaurus, Application Domain, Technology Topic, Popular Technical Reports.
© 2025 PatSnap. All rights reserved.Legal|Privacy policy|Modern Slavery Act Transparency Statement|Sitemap|About US| Contact US: help@patsnap.com