Coaxial electrospinning process of fibroin-polycaprolactone bi-component ultrafine fiber
A technology of coaxial electrospinning and polycaprolactone, applied in the direction of cellulose/protein conjugated artificial filament, fiber treatment, filament/thread forming, etc., can solve the problem of increasing the rejection probability of human organs and affecting the composite nanomaterials Fiber stability and other issues, to achieve the effect of improving coverage, simple method, and increasing stability
- Summary
- Abstract
- Description
- Claims
- Application Information
AI Technical Summary
Problems solved by technology
Method used
Image
Examples
Embodiment 1
[0019] The invention discloses a coaxial electrospinning process of silk fibroin-polycaprolactone bicomponent ultrafine fibers, which comprises the following steps:
[0020] S1: Degumming silkworm silk in 0.06% sodium carbonate solution at 98-100°C for 3 times, 30 minutes each time, then washing with deionized water for 3 times, stretching and drying in an oven at 55°C for 3 hours Obtain thick silk fibroin after drying;
[0021] According to the lithium bromide solution that every 15g silk fibroin is equipped with 100ml 9.3mol / L, above-mentioned crude silk fibroin protein is dissolved in lithium bromide solution, forms the mixed solution of silk fibroin and lithium bromide;
[0022] Dialyze the above mixed solution of silk fibroin and lithium bromide with deionized water to obtain a high-purity silkworm fibroin protein solution, then place it in a polyethylene tray and dry it at 20°C for 2 hours to make a high-purity silk fibroin film;
[0023] Dissolving the above-mentioned ...
Embodiment 2
[0029] The invention discloses a coaxial electrospinning process of silk fibroin-polycaprolactone bicomponent ultrafine fibers, which comprises the following steps:
[0030] S1: Degumming silkworm silk in 0.06% sodium carbonate solution at 98-100°C for 2 times, 30 minutes each time, then washing with deionized water for 5 times, stretching and drying in an oven at 45°C for 0.5 hours Obtain thick silk fibroin after drying;
[0031]According to the lithium bromide solution that every 15g silk fibroin is equipped with 100ml 9.3mol / L, above-mentioned crude silk fibroin protein is dissolved in lithium bromide solution, forms the mixed solution of silk fibroin and lithium bromide;
[0032] The above mixed solution of silk fibroin and lithium bromide was dialyzed with deionized water to obtain a pure silkworm fibroin protein solution, and then placed in a polyethylene tray and dried at 10°C for 4 hours to form a high-purity silk fibroin film;
[0033] Dissolving the above-mentioned ...
Embodiment 3
[0038] The invention discloses a coaxial electrospinning process of silk fibroin-polycaprolactone bicomponent ultrafine fibers, which comprises the following steps;
[0039] S1: Degumming silkworm silk in 0.06% sodium carbonate solution at 98-100°C for 5 times, 30 minutes each time, then washing with deionized water for 2 times, stretching and drying in an oven at 60°C for 4 hours Obtain thick silk fibroin after drying;
[0040] According to the lithium bromide solution that every 15g silk fibroin is equipped with 100ml 9.3mol / L, above-mentioned crude silk fibroin protein is dissolved in lithium bromide solution, forms the mixed solution of silk fibroin and lithium bromide;
[0041] The above mixed solution of silk fibroin and lithium bromide was dialyzed with deionized water to obtain a pure silkworm fibroin protein solution, and then placed in a polyethylene tray and dried at 35°C for 0.5h to form a high-purity silk fibroin film;
[0042] Dissolving the above-mentioned high...
PUM
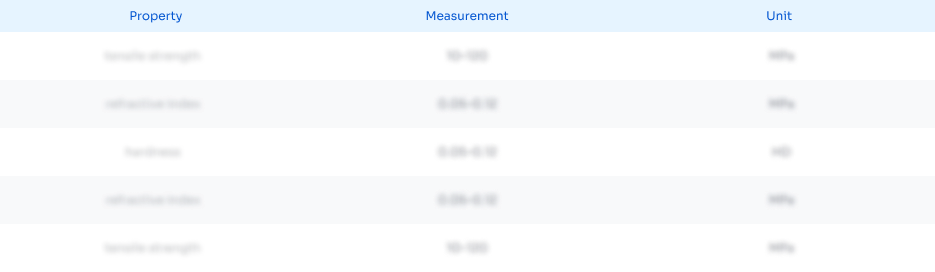
Abstract
Description
Claims
Application Information

- R&D Engineer
- R&D Manager
- IP Professional
- Industry Leading Data Capabilities
- Powerful AI technology
- Patent DNA Extraction
Browse by: Latest US Patents, China's latest patents, Technical Efficacy Thesaurus, Application Domain, Technology Topic, Popular Technical Reports.
© 2024 PatSnap. All rights reserved.Legal|Privacy policy|Modern Slavery Act Transparency Statement|Sitemap|About US| Contact US: help@patsnap.com