A method for washing converter steel using low al alumina ball slag
A technology of alumina balls and alumina, applied in the field of slag washing using low Al alumina balls in converter tapping, can solve the problems of corrosion of refractory materials, poor slag washing conditions, high cost, etc., achieve low melting point, large amount of slag, and improve Effect of slag condition
- Summary
- Abstract
- Description
- Claims
- Application Information
AI Technical Summary
Problems solved by technology
Method used
Examples
Embodiment 1
[0023] xxxQ00162 heat, aluminum-free steel type A ship plate steel, the process route adopted is: converter smelting - slag washing - ladle furnace refining - slab continuous casting.
[0024] Converter smelting: Converter end point carbon content [C] = 0.125%, end point sulfur content [S] = 0.0137%, end point temperature T = 1655°C; tapping adopts weak deoxidation and slag blocking operations.
[0025] Slag washing: when the tapping amount reaches 30% of the total amount, add lime 5.06kg / t steel and low Al alumina ball 1.5kg / t steel.
[0026] Refining in ladle furnace: blowing argon on the ladle at the refining station for 3 minutes, and the flow rate of argon gas is 800NL / min. The temperature is measured at 1567°C, and it enters the heating position for treatment, using the 9 / 1 gear to melt the slag for 1 minute. Turn to 3 / 4 gear and heat up for 15 minutes. During the process, 214kg of lime and 25kg of fluorite were added.
[0027] In terms of overall effect, the cost is ...
Embodiment 2
[0029] xxxN00107 heat, aluminum-containing plain carbon steel B-S, the process route adopted is: converter smelting - slag washing - ladle furnace refining - slab continuous casting.
[0030] Converter smelting: Converter end point carbon content [C] = 0.112wt%, end point sulfur content [S] = 0.0225%, end point temperature T = 1652°C; tapping adopts weak deoxidation and slag blocking operations.
[0031] Slag washing: when the amount of steel tapping reaches one-third of the total, add lime 4.82kg / t steel and low Al alumina ball 2.00kg / t steel.
[0032] Refining in ladle furnace: blowing argon on the ladle at the refining station for 3 minutes, and the flow rate of argon gas is 800NL / min. Measure the temperature at 1558°C, use the 9 / 1 gear to melt the slag for 1 minute, turn to the 6 / 1 gear to melt the slag for 2 minutes, and then turn to the 3 / 4 gear (voltage value 169v) to raise the temperature for 10 minutes. Add lime 5.56kg / t steel, aluminum particles 45kg / t steel, alumin...
Embodiment 3
[0035] xxx Q00112 heat, aluminum-containing low-sulfur steel S355G8+M, the process route adopted is: converter smelting - slag washing - ladle furnace refining - RH vacuum refining - slab continuous casting.
[0036] Converter smelting: Converter end point carbon content [C] = 0.039%, end point sulfur content [S] = 0.0226%, end point temperature T = 1667°C; tapping adopts strong deoxidation and slag blocking operations.
[0037] Slag washing: when the tapping amount reaches one-third of the total amount, add lime 4.12kg / t steel and low Al alumina ball 2.00kg / t steel. Aluminum and iron 4.70kg / t steel.
[0038] Refining in ladle furnace: blowing argon on the ladle at the refining station for 3 minutes, and the flow rate of argon gas is 800NL / min. The temperature was measured at 1555°C. Adjust slag remover and aluminum pellets. Fluorite 0.60-1.00kg / t steel. Enter the heating position treatment, use 9 / 1 gear for 2 minutes, turn to 6 / 1 gear for 2 minutes (voltage value 146v), t...
PUM
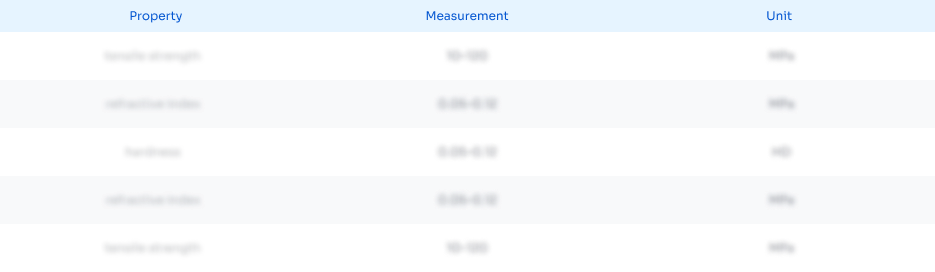
Abstract
Description
Claims
Application Information

- R&D Engineer
- R&D Manager
- IP Professional
- Industry Leading Data Capabilities
- Powerful AI technology
- Patent DNA Extraction
Browse by: Latest US Patents, China's latest patents, Technical Efficacy Thesaurus, Application Domain, Technology Topic, Popular Technical Reports.
© 2024 PatSnap. All rights reserved.Legal|Privacy policy|Modern Slavery Act Transparency Statement|Sitemap|About US| Contact US: help@patsnap.com