Malononitrile synthesis method
A synthesis method and technology of malononitrile, applied in the field of chemical synthesis and synthesis of malononitrile, can solve the problems of large amount of solvent and adsorbent, difficult separation of by-product phosphoric acid, high safety risk, etc., and achieve few reaction steps and high product quality Good purity and the effect of reducing the amount of three wastes
- Summary
- Abstract
- Description
- Claims
- Application Information
AI Technical Summary
Problems solved by technology
Method used
Image
Examples
Embodiment 1
[0035] (1) In a 5000ml four-necked flask, add 3000ml methanol, cool down to -5°C~0°C in an ice-salt bath, feed ammonia gas to saturation, control the temperature at 10~15°C, add 1000g methyl cyanoacetate dropwise, add dropwise After the completion, the reaction was carried out with heat preservation and stirring for 4 hours. Sampling was carried out to control the reaction of methyl cyanoacetate. The reaction of methyl cyanoacetate was basically complete. The ammonia gas was decompressed until the temperature dropped below -10°C. Then, it was filtered by suction and dried to obtain 822g, with a yield of 97.9%.
[0036] (2) In a 1000ml four-neck flask, add 168g cyanoacetamide, 500g1,2-dichloroethane, catalyst and 170g phosphorus oxychloride, heat and reflux for 6 hours, cool down to room temperature, filter with suction, and use 200g1 , washed with 2-dichloroethane, drained, and the filtrate was desolvated to obtain a crude product. Then, 122 g of malononitrile was obtained by v...
Embodiment 2
[0038] (1) In a 5000ml four-neck flask, add 3000ml of methanol, cool down in an ice-salt bath to 0°C-5°C, feed ammonia gas to saturation, control the temperature at 0-5°C, add 1000g of methyl cyanoacetate dropwise, and the dropwise addition is completed Afterwards, heat-preserve and stir for 4 hours, take a sample to control, the reaction of methyl cyanoacetate is basically complete, remove ammonia gas under reduced pressure until the temperature drops below -10°C, filter with suction, and dry to obtain 818g, with a yield of 97.4%.
[0039] (2) In a 1000ml four-neck flask, add 168g cyanoacetamide, 500g cyclohexane, catalyst and 170g phosphorus oxychloride, heat and reflux for 6 hours, cool down to room temperature, filter with suction, and wash the filter cake with 200g cyclohexane , pumped to dryness, and the filtrate was desolvated to obtain a crude product. Then, oil pump vacuum distillation gave 125 g of malononitrile, with a yield of 94.7%.
Embodiment 3
[0041] (1) In a 5000ml four-neck flask, add 3000ml methanol, cool down in an ice-salt bath to 20°C-30°C, feed ammonia gas to saturation, control the temperature at 20-30°C, add 1000g methyl cyanoacetate dropwise, and dropwise complete Afterwards, heat-preserved and stirred for 4 hours to react. Sampling was carried out to control the reaction of methyl cyanoacetate. The reaction of methyl cyanoacetate was basically complete. The ammonia gas was decompressed until the temperature dropped below -10°C. Then, it was filtered by suction and dried to obtain 803g, with a yield of 95.6%.
[0042](2) In a 1000ml four-neck flask, add 168g cyanoacetamide, 500g1,2-dichloroethane, catalyst and 230g phosphorus oxychloride, heat and reflux for 6 hours, cool down to room temperature, filter with suction, and use 200g1 , washed with 2-dichloroethane, drained, and the filtrate was desolvated to obtain a crude product. Then, 123 g of malononitrile was obtained by vacuum distillation with an oil p...
PUM
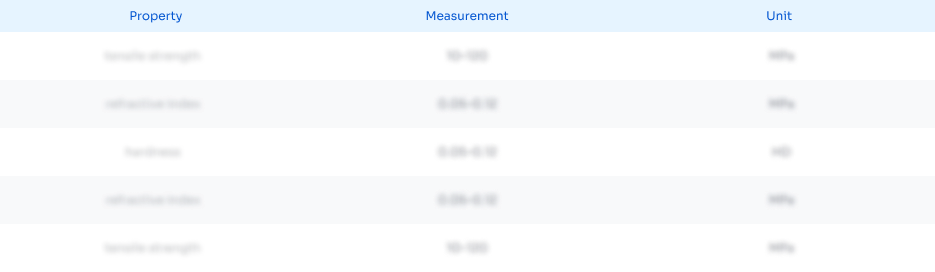
Abstract
Description
Claims
Application Information

- R&D
- Intellectual Property
- Life Sciences
- Materials
- Tech Scout
- Unparalleled Data Quality
- Higher Quality Content
- 60% Fewer Hallucinations
Browse by: Latest US Patents, China's latest patents, Technical Efficacy Thesaurus, Application Domain, Technology Topic, Popular Technical Reports.
© 2025 PatSnap. All rights reserved.Legal|Privacy policy|Modern Slavery Act Transparency Statement|Sitemap|About US| Contact US: help@patsnap.com