Preparing method of PS (polystyrene) composite
A technology of polystyrene and composite materials, applied in the field of preparation of polystyrene composite materials, can solve the problems of obvious low temperature brittleness, poor impact resistance, stress cracking, etc., to enhance impact resistance and toughness, avoid stress cracking, improve rigid effect
- Summary
- Abstract
- Description
- Claims
- Application Information
AI Technical Summary
Problems solved by technology
Method used
Examples
Embodiment 1
[0016] Embodiment 1: a kind of preparation method of polystyrene composite material, comprises the following steps:
[0017] (1) Prepare the following ingredients, by mass percentage: polystyrene (PS) 65%, modified resin filler 34%, antioxidant 0.3%, lubricant 0.3%, additive 0.4%;
[0018] (2) Air-dry polystyrene (PS) and modified resin filler at 75°C for 7 hours;
[0019] (3) Cool the dry polystyrene (PS) obtained in step 2 and the modified resin filler to room temperature and place them in a high mixer to mix them evenly with antioxidants, lubricants and additives to obtain a premix;
[0020] (4) Put the premixed material obtained in step 3 in a twin-screw extruder to melt, extrude, and granulate to obtain the product. The process conditions for melt extrusion and granulation: the temperature in the first zone is 170°C, the temperature in the second zone is 200°C, and the temperature in the third zone 215°C, the temperature of the fourth zone is 220°C, the temperature of th...
Embodiment 2
[0022] Embodiment 2: a kind of preparation method of polystyrene composite material, comprises the following steps:
[0023] (1) Prepare the following ingredients, by mass percentage: polystyrene (PS) 89%, modified resin filler 10%, antioxidant 0.3%, lubricant 0.3%, additive 0.4%;
[0024] (2) Air-dry polystyrene (PS) and modified resin filler at 85°C for 4 hours;
[0025] (3) Cool the dry polystyrene (PS) obtained in step 2 and the modified resin filler to room temperature and place them in a high mixer to mix them evenly with antioxidants, lubricants and additives to obtain a premix;
[0026] (4) Put the premixed material obtained in step 3 in a twin-screw extruder to melt and extrude to obtain the product. The process conditions of melt extrusion and granulation: the temperature of the first zone is 200°C, the temperature of the second zone is 215°C, and the temperature of the third zone 225°C, the temperature of the fourth zone is 230°C, the temperature of the fifth zone ...
Embodiment 3
[0028] Embodiment 3: a kind of preparation method of polystyrene composite material, comprises the following steps:
[0029] (1) Prepare the following ingredients, by mass percentage: polystyrene (PS) 78%, modified resin filler 20%, antioxidant 0.4%, lubricant 0.4%, additive 1.2%;
[0030] (2) Air-dry polystyrene (PS) and modified resin filler at 80°C for 5 hours;
[0031] (3) Cool the dry polystyrene (PS) obtained in step 2 and the modified resin filler to room temperature and place them in a high mixer to mix them evenly with antioxidants, lubricants and additives to obtain a premix;
[0032] (4) Put the premixed material obtained in step 3 in a twin-screw extruder to melt and extrude to obtain the product. The process conditions of melt extrusion and granulation: the temperature of the first zone is 185°C, the temperature of the second zone is 210°C, and the temperature of the third zone 220°C, the temperature of the fourth zone is 225°C, the temperature of the fifth zone ...
PUM
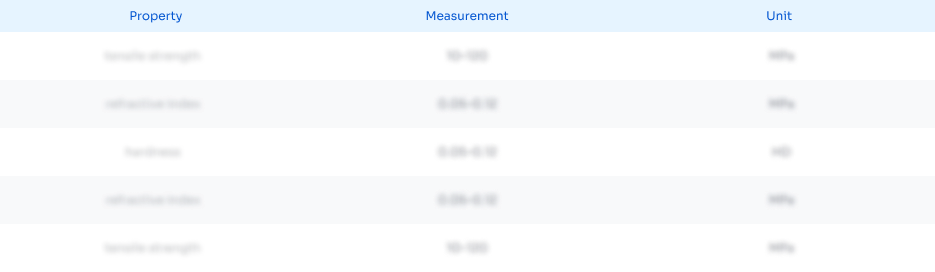
Abstract
Description
Claims
Application Information

- R&D
- Intellectual Property
- Life Sciences
- Materials
- Tech Scout
- Unparalleled Data Quality
- Higher Quality Content
- 60% Fewer Hallucinations
Browse by: Latest US Patents, China's latest patents, Technical Efficacy Thesaurus, Application Domain, Technology Topic, Popular Technical Reports.
© 2025 PatSnap. All rights reserved.Legal|Privacy policy|Modern Slavery Act Transparency Statement|Sitemap|About US| Contact US: help@patsnap.com