Production method for avoiding inner wall cracks of double-layer alloy composite pipe
A production method and technology for composite pipes, which are applied in the directions of pipes, rigid pipes, pipes/pipe joints/fittings, etc., can solve problems such as cracks on the inner wall of double-layer alloy composite pipes, and achieve difficult delamination cracking, crack prevention, and high bonding strength. Effect
- Summary
- Abstract
- Description
- Claims
- Application Information
AI Technical Summary
Problems solved by technology
Method used
Image
Examples
Embodiment 1
[0025] In the embodiment of the present invention, the material of the composite pipe is 15Mn / 316L, the material of the outer layer is 15Mn, and the material of the inner layer is 316L. The chemical composition of the outer layer and the inner layer meets the requirements of Table 1, and the specification is φ133mm×16mm / (outer layer 10mm+inner Layer 6mm) × 5000mm.
[0026] Table 1 Composition / mass fraction of 15Mn / 316L composite pipe (%)
[0027]
[0028] The specific production steps are as follows:
[0029] (1) Centrifugal casting double-layer alloy composite hollow billet
[0030] Smelt the outer layer 15Mn and inner layer 316L alloy liquid of the finished pipe respectively, pour the outer layer 15Mn first on the centrifugal casting machine, and then pour the inner layer 316L to prepare a double-layer alloy composite hollow billet. The specification of the composite pipe billet is φ250mm×80mm / (43.37mm outer layer + 36.63mm inner layer) × 1000mm.
[0031] The specifi...
Embodiment 2
[0045] The material of the composite pipe is 20Mn2 / 825, the material of the outer layer is 20Mn2, and the material of the inner layer is 825. The chemical composition of the outer layer and the inner layer meets the requirements in Table 2, and the specification is φ273mm×16.5mm / (outer layer 11mm+inner layer 5.5mm)× 6000mm.
[0046] Table 2 Composition / mass fraction of 20Mn2 / 825 composite pipe (%)
[0047]
[0048] The specific production steps are as follows:
[0049] (1) Centrifugal casting double-layer alloy composite hollow billet
[0050] Smelt the outer layer 20Mn2 and the inner layer 825 alloy liquid of the finished pipe respectively, cast the outer layer 20Mn2 first on the centrifugal casting machine, and then pour the inner layer 825 to prepare a double-layer alloy composite hollow billet. The specification of the double-layer alloy composite hollow billet is φ429mm×124.5mm / (outer layer 71.16mm+inner layer 53.34mm)×910mm.
[0051] The specific pouring process is...
PUM
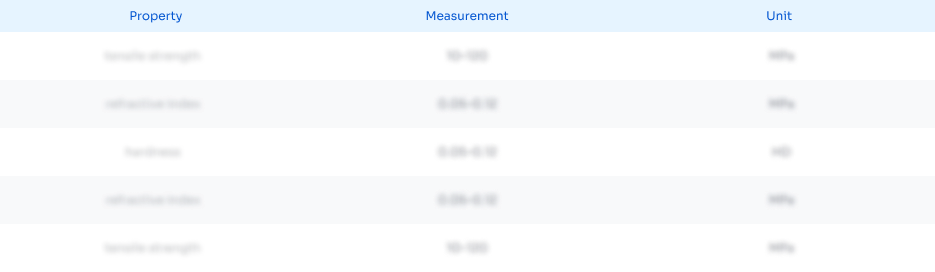
Abstract
Description
Claims
Application Information

- R&D Engineer
- R&D Manager
- IP Professional
- Industry Leading Data Capabilities
- Powerful AI technology
- Patent DNA Extraction
Browse by: Latest US Patents, China's latest patents, Technical Efficacy Thesaurus, Application Domain, Technology Topic, Popular Technical Reports.
© 2024 PatSnap. All rights reserved.Legal|Privacy policy|Modern Slavery Act Transparency Statement|Sitemap|About US| Contact US: help@patsnap.com