Integral quenched steel corner back gouging test piece and high-speed milling process method thereof
A high-speed milling and hardening steel technology, applied in milling machine equipment, manufacturing tools, metal processing and other directions, can solve the problem of uneven surface morphology of corner cleaning and root processing, and achieve the effect of meeting the needs of efficient processing
- Summary
- Abstract
- Description
- Claims
- Application Information
AI Technical Summary
Problems solved by technology
Method used
Image
Examples
Embodiment Construction
[0034] refer to Figure 1 to Figure 3, the integral hardened steel corner cleaning test piece includes a milling processing area 1 and a base 2 at the bottom thereof, the top surface of the milling processing area 1 is a top concave surface 3 with a curvature radius of 200mm along the width direction, so The top concave surface 3 is composed of 5 sections distributed along the length direction and have different curvature radii and are sequentially connected by smooth transition. The four corners of the top concave surface 3 are arc corners 5 with different radii. On the side elevation, there is a side concave curved surface 4 that is sunken toward its center. On the side elevation of the milling processing area 1, a peripheral convex platform 6 is formed below the side concave curved surface 4. The surface of the peripheral convex platform 6 is parallel to the top surface concave curved surface 3. The upper edge of the side concave curved surface 4 intersects the edge of the ...
PUM
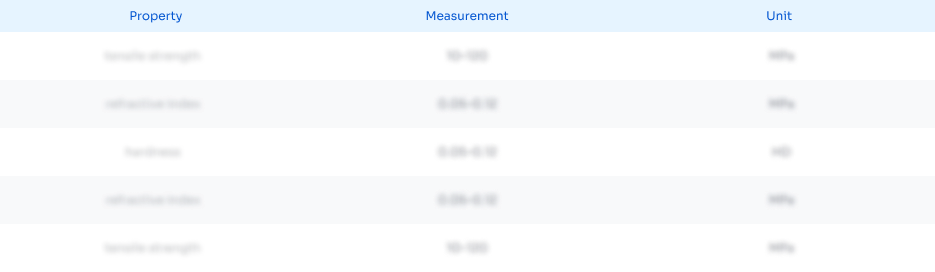
Abstract
Description
Claims
Application Information

- R&D Engineer
- R&D Manager
- IP Professional
- Industry Leading Data Capabilities
- Powerful AI technology
- Patent DNA Extraction
Browse by: Latest US Patents, China's latest patents, Technical Efficacy Thesaurus, Application Domain, Technology Topic, Popular Technical Reports.
© 2024 PatSnap. All rights reserved.Legal|Privacy policy|Modern Slavery Act Transparency Statement|Sitemap|About US| Contact US: help@patsnap.com