Sensorless control method of permanent magnet synchronous motor in wide rotating speed scope
A technology of permanent magnet synchronous motor and control method, which is applied in the direction of motor generator control, AC motor control, electronic commutation motor control, etc., and can solve the problems of large speed estimation error, easy switching failure, large speed fluctuation, etc.
- Summary
- Abstract
- Description
- Claims
- Application Information
AI Technical Summary
Problems solved by technology
Method used
Image
Examples
Embodiment Construction
[0047] The technical solution of the invention will be described in detail below in conjunction with the accompanying drawings, taking the surface-mounted permanent magnet synchronous motor as an example.
[0048] The method for the positionless composite control of the surface-mounted permanent magnet synchronous motor with a wide speed range provided by the present invention is as follows: figure 1 As shown, first, build the figure 2 The coordinate system relationship diagram shown, d-q is the actual synchronous rotation coordinate system, In order to estimate the rotor synchronous rotating coordinate system, α-β is the actual two-phase stationary coordinate system, and define the estimated position error θ is the actual rotor position, To estimate the rotor position, it specifically includes the following steps:
[0049] Step 1. Detect any two-phase current in the three-phase windings A, B, and C of the motor, and first perform Clarke transformation to obtain the act...
PUM
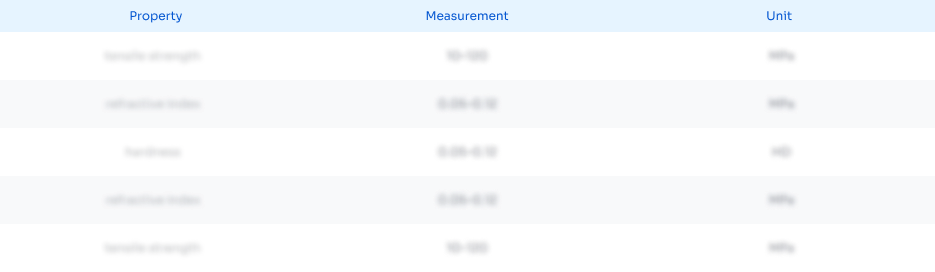
Abstract
Description
Claims
Application Information

- Generate Ideas
- Intellectual Property
- Life Sciences
- Materials
- Tech Scout
- Unparalleled Data Quality
- Higher Quality Content
- 60% Fewer Hallucinations
Browse by: Latest US Patents, China's latest patents, Technical Efficacy Thesaurus, Application Domain, Technology Topic, Popular Technical Reports.
© 2025 PatSnap. All rights reserved.Legal|Privacy policy|Modern Slavery Act Transparency Statement|Sitemap|About US| Contact US: help@patsnap.com