Cleaning agent for cleaning finished part after machining
A technology for machining and cleaning agents, applied in the field of cleaning agents, can solve problems such as reduced precision of parts or equipment, limited cleaning capacity, and impact on product quality and output.
- Summary
- Abstract
- Description
- Claims
- Application Information
AI Technical Summary
Problems solved by technology
Method used
Image
Examples
Embodiment 1
[0011] Weigh each raw material respectively, and then mix and prepare respectively: nonionic surfactant, anionic surfactant, builder, defoamer, corrosion inhibitor, solubilizer and fatty acid; first, quantitative deionized water is heated to 50 ℃, add builder, corrosion inhibitor, defoamer, fatty acid and solubilizer in sequence under stirring and mix well, then cool to 40 ℃, then add nonionic surfactant and anionic surfactant and stir well, the prepared The cleaning agent is a uniform and transparent liquid.
[0012] The specific composition of cleaning agent is: 5 parts by weight of lauryl amine polyoxyethylene ether, 1.5 parts by weight of coconut oil fatty acid diethanolamide, 2 parts by weight of lauryl betaine, 1.5 parts by weight of lauryl Glucoside, 5 parts by weight of sodium dodecylbenzenesulfonate, 4 parts by weight of sodium dodecyl diphenyl ether disulfonate, 3 parts by weight of Na-CP 4 , 0.15 parts by weight of sodium metasilicate, 0.8 parts by weight of disodi...
Embodiment 2
[0014] Weigh each raw material respectively, and then mix and prepare respectively: nonionic surfactant, anionic surfactant, builder, defoamer, corrosion inhibitor, solubilizer and fatty acid; first, quantitative deionized water is heated to 50 ℃, add builder, corrosion inhibitor, defoamer, fatty acid and solubilizer in sequence under stirring and mix well, then cool to 40 ℃, then add nonionic surfactant and anionic surfactant and stir well, the prepared The cleaning agent is a uniform and transparent liquid.
[0015] The specific composition of the cleaning agent is: 8 parts by weight of lauryl amine polyoxyethylene ether, 1 part by weight of coconut oil fatty acid diethanolamide, 3 parts by weight of lauryl betaine, 1 part by weight of lauryl Glucoside, 8 parts by weight of sodium dodecylbenzenesulfonate, 3 parts by weight of sodium dodecyl diphenyl ether disulfonate, 3.5 parts by weight of Na-CP 4 , 0.1 parts by weight of sodium metasilicate, 1.0 parts by weight of disodiu...
Embodiment 3
[0017] Weigh each raw material respectively, and then mix and prepare respectively: nonionic surfactant, anionic surfactant, builder, defoamer, corrosion inhibitor, solubilizer and fatty acid; first, quantitative deionized water is heated to 50 ℃, add builder, corrosion inhibitor, defoamer, fatty acid and solubilizer in sequence under stirring and mix well, then cool to 40 ℃, then add nonionic surfactant and anionic surfactant and stir well, the prepared The cleaning agent is a uniform and transparent liquid.
[0018] The specific composition of cleaning agent is: 6 parts by weight of lauryl amine polyoxyethylene ether, 1.2 parts by weight of coconut oil fatty acid diethanolamide, 2.5 parts by weight of lauryl betaine, 1 part by weight of lauryl Glucoside, the sodium dodecylbenzenesulfonate of 6 parts by weight, the sodium dodecyl diphenyl ether disulfonate of 4 parts by weight, the Na-CP of 3 parts by weight 4 , 0.1 parts by weight of sodium metasilicate, 0.8 parts by weight...
PUM
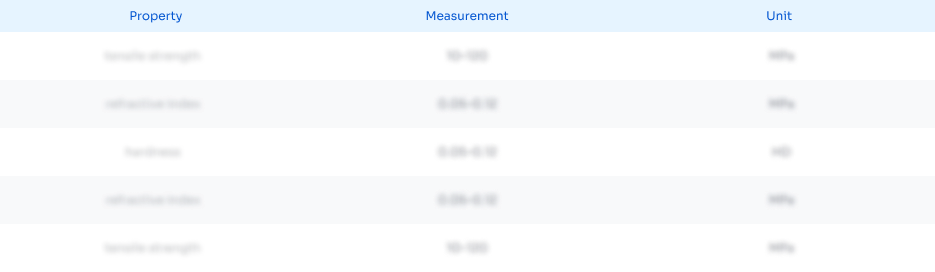
Abstract
Description
Claims
Application Information

- R&D
- Intellectual Property
- Life Sciences
- Materials
- Tech Scout
- Unparalleled Data Quality
- Higher Quality Content
- 60% Fewer Hallucinations
Browse by: Latest US Patents, China's latest patents, Technical Efficacy Thesaurus, Application Domain, Technology Topic, Popular Technical Reports.
© 2025 PatSnap. All rights reserved.Legal|Privacy policy|Modern Slavery Act Transparency Statement|Sitemap|About US| Contact US: help@patsnap.com