Stainless steel product surface passivation method
A technology for stainless steel products, applied in the coating process of metal materials, etc., can solve the problems of high content of main acid and oxidant, complex passivation process, high reagent content, etc., achieve low main composition content, good corrosion resistance, and easy operation simple effect
- Summary
- Abstract
- Description
- Claims
- Application Information
AI Technical Summary
Problems solved by technology
Method used
Image
Examples
Embodiment 1
[0021] 1. Stainless steel surface pretreatment:
[0022] Firstly, the 304 stainless steel sheet with regular cuts was placed in a 65°C cleaning agent for ultrasonic cleaning for 6 minutes. During the cleaning process, the surface of the steel sheet should be fully cleaned. The composition of the cleaning agent includes sodium hydroxide, sulfosalicylic acid, non-ionic surfactant NP-10, coconut oil fatty acid diethanolamide 6501, sodium polyphosphate, etc., and then put the 304 stainless steel sheet into deionized water for ultrasonic cleaning 2 -3 min, dry with hot air, and set aside.
[0023] 2. Configure passivation solution:
[0024] from citric acid (C 6 h 8 o 7 , analytically pure), hydrogen peroxide (H 2 o 2 , analytically pure) and ethylene glycol (HOCH 2 CH 2 OH, analytically pure) was dissolved in deionized water in proportion to form a passivation solution containing 0.5% citric acid, 2% hydrogen peroxide, 0.5% ethylene glycol, and 97% deionized water.
[002...
Embodiment 2
[0028] 1. Surface pretreatment of stainless steel: take the stainless steel material and process it in the same way as in step 1 of embodiment 1.
[0029] 2. Configure passivation solution:
[0030] from citric acid (C 6 h 8 o 7 , analytically pure), hydrogen peroxide (H 2 o 2 , analytically pure) and ethylene glycol (HOCH 2 CH 2 OH, analytically pure) was dissolved in deionized water in proportion to form a passivation solution with 0.5% citric acid, 0.5% hydrogen peroxide, 0.5% ethylene glycol, and 98.5% deionized water.
[0031] 3. Put the stainless steel material obliquely into the prepared 30 ℃ passivation solution to ensure full contact between the stainless steel sheet and the passivation solution, and take out the stainless steel material after 120 minutes.
[0032] 4. Ultrasonic clean the passivated stainless steel in step 3 with deionized water at room temperature for 2 to 3 minutes, and then dry it with hot air to obtain the stainless steel with passivation f...
Embodiment 3
[0034] 1. Surface pretreatment of stainless steel parts: get the stainless steel parts and process with the method of step 1 of embodiment 1.
[0035] 2. Configure passivation solution:
[0036] from citric acid (C 6 h 8 o 7 , analytically pure), hydrogen peroxide (H 2 o 2 , analytically pure) and ethylene glycol (HOCH 2 CH 2 OH, analytically pure) was dissolved in deionized water in proportion to form a passivation solution containing 0.5% citric acid, 2% hydrogen peroxide, 0.5% ethylene glycol, and 97% deionized water.
[0037] 3. Immerse the stainless steel parts in the prepared 60 ℃ passivation solution, and take out the stainless steel parts after 90 minutes.
[0038] 4. Ultrasonic clean the stainless steel parts with deionized water for 2-3 minutes at room temperature, and then dry them with hot air to obtain stainless steel parts with a passivation film, and pack them into bags for later use.
[0039] The configuration of the passivation solution and the tempera...
PUM
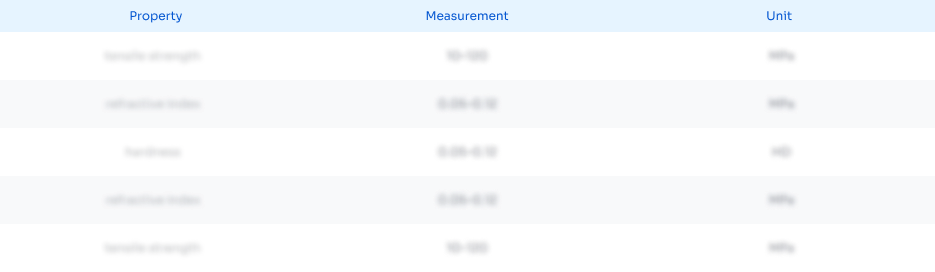
Abstract
Description
Claims
Application Information

- Generate Ideas
- Intellectual Property
- Life Sciences
- Materials
- Tech Scout
- Unparalleled Data Quality
- Higher Quality Content
- 60% Fewer Hallucinations
Browse by: Latest US Patents, China's latest patents, Technical Efficacy Thesaurus, Application Domain, Technology Topic, Popular Technical Reports.
© 2025 PatSnap. All rights reserved.Legal|Privacy policy|Modern Slavery Act Transparency Statement|Sitemap|About US| Contact US: help@patsnap.com