A welding method of q690 high-strength steel pipes for the truss arm of a large offshore crane
A welding method and truss arm technology, applied in welding equipment, welding/welding/cutting items, applications, etc., can solve the problem of decreased material strength and toughness at joints, large amount of assembly misalignment, and main chord steel pipe out-of-roundness deviation. It can achieve the effect of inhibiting softening and microstructure embrittlement, good fatigue resistance and simple welding process.
- Summary
- Abstract
- Description
- Claims
- Application Information
AI Technical Summary
Problems solved by technology
Method used
Image
Examples
Embodiment Construction
[0039] The present invention will be described in detail below in conjunction with the accompanying drawings.
[0040] Such as figure 1 As shown, the welding method of the Q690 high-strength steel pipe for the truss arm of the large-scale offshore crane of the present invention is characterized in that, comprising the following steps:
[0041] The first step is to make the liner 2 according to the inner diameter of the steel pipe to be welded;
[0042] The above-mentioned liner is a one-piece structure with two ends thin and the middle thick, approximately spinning cone-shaped, and it includes three parts: the left end, the middle part and the right end, wherein the left end and the right end are symmetrically distributed on the left and right sides of the middle part, And respectively with the middle part;
[0043] The shape of the above-mentioned middle part is a cylinder, and the above-mentioned left end and right end are respectively circular truncated with thin ends fac...
PUM
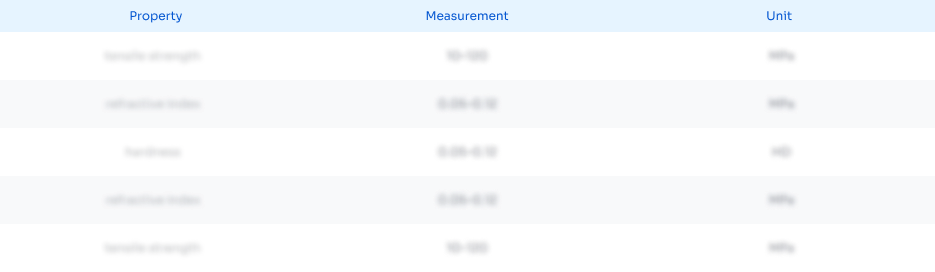
Abstract
Description
Claims
Application Information

- R&D Engineer
- R&D Manager
- IP Professional
- Industry Leading Data Capabilities
- Powerful AI technology
- Patent DNA Extraction
Browse by: Latest US Patents, China's latest patents, Technical Efficacy Thesaurus, Application Domain, Technology Topic, Popular Technical Reports.
© 2024 PatSnap. All rights reserved.Legal|Privacy policy|Modern Slavery Act Transparency Statement|Sitemap|About US| Contact US: help@patsnap.com