Composite wet strength agent and production method thereof
A technology of wet strength agent and mixture, which is applied in the field of composite wet strength agent and its production, which can solve the problems of environmental pollution, harmful substances, and harm to human health, and achieve the effects of improving wet strength, enhancing affinity, and enhancing cohesion
- Summary
- Abstract
- Description
- Claims
- Application Information
AI Technical Summary
Problems solved by technology
Method used
Image
Examples
Embodiment 1
[0021] In the embodiment of the present invention, a composite wet strength agent comprises raw materials according to mass percentage: 5 parts of polyamide epichlorohydrin, 3.5 parts of sodium lauryl sulfate, 7 parts of hydroxyethyl hexadecane cellulose, mono 8 parts of potassium dodecyl phosphate, 7 parts of p-toluenesulfonic acid, 11 parts of polyethylene glycol, 12 parts of urea, 6 parts of diethylenetriamine, 7 parts of cyclohexane, 4 parts of sodium sulfamate, 0.5 part of dicarboxylate half ester, 8 parts of dodecyltrimethylammonium chloride and 21 parts of water.
[0022] The production method of described composite wet strength agent, comprises the following steps:
[0023] (1) Weigh polyamide epichlorohydrin, sodium lauryl sulfate, hydroxyethyl hexadecyl cellulose, potassium monododecyl phosphate, p-toluenesulfonic acid and polyethylene glycol in proportion , mixed, stirred and reacted for 0.8h, and the stirring speed was 110r / min;
[0024] (2) Weigh and mix urea, d...
Embodiment 2
[0028] In the embodiment of the present invention, a composite wet strength agent, raw materials according to mass percentages include: 6 parts of polyamide epichlorohydrin, 4 parts of sodium lauryl sulfate, 6 parts of hydroxyethyl hexadecane cellulose, mono 9 parts of potassium dodecyl phosphate, 6 parts of p-toluenesulfonic acid, 10 parts of polyethylene glycol, 13 parts of urea, 7 parts of a mixture of diethylenetriamine and triethylenetetramine with a mass ratio of 1:1, 8 parts of cyclohexane, 4.5 parts of sodium sulfamate, 1 part of dihydrocarbyl methylpropionic acid, 7.5 parts of dodecyltrimethylammonium chloride and 18 parts of water.
[0029] The production method of described composite wet strength agent, comprises the following steps:
[0030] (1) Weigh polyamide epichlorohydrin, sodium lauryl sulfate, hydroxyethyl hexadecyl cellulose, potassium monododecyl phosphate, p-toluenesulfonic acid and polyethylene glycol in proportion , mixed, stirred and reacted for 1.2h,...
Embodiment 3
[0035] In the embodiment of the present invention, a composite wet strength agent, raw materials according to mass percentages include: 8 parts of polyamide epichlorohydrin, 3.5 parts of sodium lauryl sulfate, 4 parts of hydroxyethyl hexadecane cellulose, mono 10 parts of potassium dodecyl phosphate, 5 parts of p-toluenesulfonic acid, 8 parts of polyethylene glycol, 15 parts of urea, 8 parts of tetraethylenepentamine, 7 parts of cyclohexane, 5 parts of sodium sulfamate, 1.5 parts of dihydrocarbyl methylpropionic acid, 7 parts of dodecyltrimethylammonium chloride and 18 parts of water.
[0036] The production method of described composite wet strength agent, comprises the following steps:
[0037] (1) Weigh polyamide epichlorohydrin, sodium lauryl sulfate, hydroxyethyl hexadecyl cellulose, potassium monododecyl phosphate, p-toluenesulfonic acid and polyethylene glycol in proportion , mixed, stirred and reacted for 1.5h, the stirring speed was 100r / min;
[0038] (2) Weigh and ...
PUM
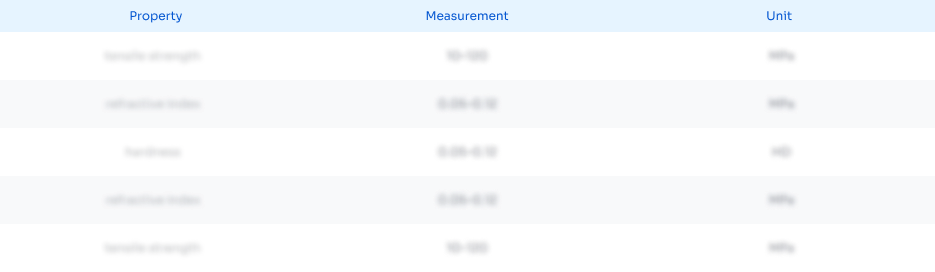
Abstract
Description
Claims
Application Information

- R&D Engineer
- R&D Manager
- IP Professional
- Industry Leading Data Capabilities
- Powerful AI technology
- Patent DNA Extraction
Browse by: Latest US Patents, China's latest patents, Technical Efficacy Thesaurus, Application Domain, Technology Topic, Popular Technical Reports.
© 2024 PatSnap. All rights reserved.Legal|Privacy policy|Modern Slavery Act Transparency Statement|Sitemap|About US| Contact US: help@patsnap.com