Preparation method and device of polyethylene molten spun filament of ultra-high molecular weight
An ultra-high molecular weight, melt-spinning technology, which is applied in the field of melt-spinning, can solve problems such as uneven thread thickness, molecular rearrangement, and inability to ensure uniform molecular arrangement, so as to ensure the melting effect and simple process Effect
- Summary
- Abstract
- Description
- Claims
- Application Information
AI Technical Summary
Problems solved by technology
Method used
Image
Examples
Embodiment 1
[0024] Such as figure 1 Shown, the preparation method and device of ultra-high molecular weight polyethylene melt spinning,
[0025] (1) Raw material extrusion treatment: the raw material is extruded to the melting zone through the sleeve-type die, and the inside of the sleeve-type die is vacuum. The sleeve-type die includes a sleeve and a screw inside the sleeve. There are several rifling lines, and the end of the sleeve is extended with a melting zone and a dense zone. The inside of the sleeve is a vacuum, and the temperature of the melting zone is 350 degrees. Under the continuous extrusion of subsequent raw materials, the melted raw materials pass through the dense zone. The wire hole at the lower end of the tube is extruded into a wire, and the dense area is a bent tube whose radius decreases linearly to the lower end;
[0026] (2) Silk thread curing treatment: the silk thread is cured by a warm water tank, and the water temperature in the warm water tank is 50 degrees. ...
Embodiment 2
[0030] Such as figure 2 Shown, the preparation method and device of ultra-high molecular weight polyethylene melt spinning,
[0031] (1) Raw material extrusion treatment: the raw material is extruded to the melting zone through the sleeve-type head. The sleeve-type head includes a sleeve and a screw inside the sleeve. There is a melting zone and a dense zone extending from the inside of the sleeve. The inside of the sleeve is vacuum, and the temperature of the melting zone is 360 degrees. Under the continuous extrusion of subsequent raw materials, the melted raw materials are extruded into silk threads through the outlet hole at the lower end of the dense zone. , the dense area is a bent tube and its radius decreases linearly to the lower end.
[0032] (2) Silk thread curing treatment: the silk thread is cured by a warm water tank, and the water temperature in the warm water tank is 50 degrees.
[0033] (3) Silk thread stretching treatment: the thread treated in step (2) is...
PUM
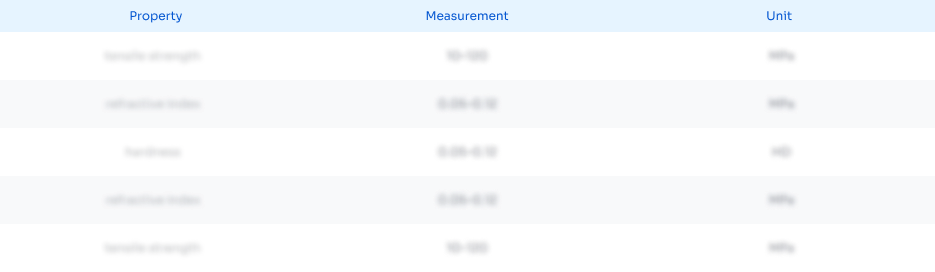
Abstract
Description
Claims
Application Information

- Generate Ideas
- Intellectual Property
- Life Sciences
- Materials
- Tech Scout
- Unparalleled Data Quality
- Higher Quality Content
- 60% Fewer Hallucinations
Browse by: Latest US Patents, China's latest patents, Technical Efficacy Thesaurus, Application Domain, Technology Topic, Popular Technical Reports.
© 2025 PatSnap. All rights reserved.Legal|Privacy policy|Modern Slavery Act Transparency Statement|Sitemap|About US| Contact US: help@patsnap.com