Smelting method for low-carbon low-silicon wire-welding steel
A low-carbon, low-silicon, welding wire steel technology, applied in the manufacture of converters, etc., can solve the problems of many billets with bubbles, clogging of continuous casting nozzles, etc., and achieve the effects of good welding performance, fewer pinholes, and good quality.
- Summary
- Abstract
- Description
- Claims
- Application Information
AI Technical Summary
Problems solved by technology
Method used
Examples
Embodiment 1
[0033] Low-carbon low-silicon welding wire steel H08E, its smelting process steps are:
[0034] 1) The molten iron is pretreated by spraying granular magnesium desulfurization, the sulfur content of the molten iron is 0.011%, and the slag removal operation is carried out;
[0035] 2) Control requirements for tapping composition at the end of the converter: C: 0.04%, Si: 0.002%, P: 0.011%, S: 0.027%; tapping temperature 1624°C; deoxidation alloying during tapping, order and weight of alloy addition For: 4.5kg / t low-carbon manganese is added after tapping 1 / 3, 0.45kg / t aluminum ingot and 0.85kg / t silicon-calcium-barium are added to tapping 2 / 3; scum.
[0036]3) The oxygen content of the LF furnace entering the station is 0.0030%, no need to add ferroaluminum manganese, and the quality of the slagging material added afterwards is: lime 7.05kg / t steel, wollastonite 5.6kg / t steel, fluorite 0.6kg / t steel During the refining process, calcium carbide is added to the slag surface sev...
Embodiment 2
[0040] Low-carbon low-silicon welding wire steel H08E, its smelting process steps are:
[0041] 1) The molten iron is pretreated by spraying granular magnesium desulfurization, the sulfur content of the molten iron is 0.007%, and the slag removal operation is carried out;
[0042] 2) Control requirements for tapping composition at the end of the converter: C: 0.04%, Si: 0.002%, P: 0.013%, S: 0.026%; tapping temperature 1641°C; deoxidation alloying during tapping, order and weight of alloys added It is: add 4.6kg / t low-carbon manganese after tapping 1 / 3, add 0.52kg / t aluminum ingot and 0.95kg / t silicon-calcium-barium to tap 2 / 3; scum.
[0043] 3) The oxygen content of the LF furnace entering the station is 0.0030%, no need to add ferroaluminum manganese, and the quality of the slagging material added afterwards is: lime 7.2kg / t steel, wollastonite 5.7kg / t steel, fluorite 0.85kg / t; During the refining process, calcium carbide is added to the slag surface several times, the tot...
Embodiment 3
[0047] Low-carbon low-silicon welding wire steel H08E, its smelting process steps are:
[0048] 1) The molten iron is pretreated by spraying granular magnesium desulfurization, the sulfur content of the molten iron is 0.012%, and the slag removal operation is carried out;
[0049] 2) Control requirements for tapping composition at the end of the converter: C: 0.043%, Si: 0.001%, P: 0.011%, S: 0.022%; tapping temperature 1637°C; deoxidation alloying during tapping, order and weight of alloys added It is: add 4.4kg / t low-carbon manganese after tapping 1 / 3, add 0.55kg / t aluminum ingot and 1.02kg / t silicon-calcium-barium after tapping 2 / 3; scum.
[0050] 3) The oxygen content of the LF furnace entering the station is 0.0050%, and 30kg of ferro-aluminum manganese is added, and then the amount of slagging material added is: lime 7.1kg / t steel, wollastonite 5.6kg / t steel, fluorite 0.9kg / t t steel; during the refining process, calcium carbide was added to the slag surface several ti...
PUM
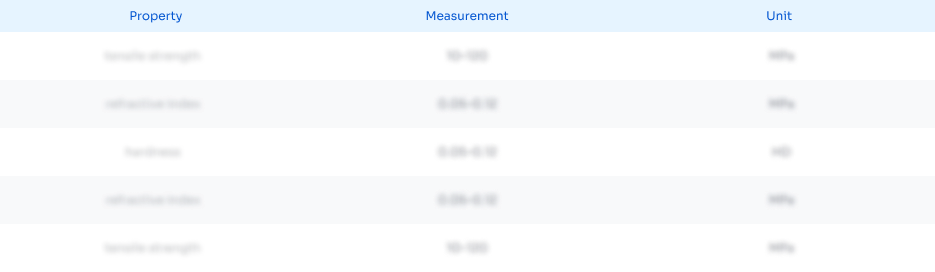
Abstract
Description
Claims
Application Information

- R&D
- Intellectual Property
- Life Sciences
- Materials
- Tech Scout
- Unparalleled Data Quality
- Higher Quality Content
- 60% Fewer Hallucinations
Browse by: Latest US Patents, China's latest patents, Technical Efficacy Thesaurus, Application Domain, Technology Topic, Popular Technical Reports.
© 2025 PatSnap. All rights reserved.Legal|Privacy policy|Modern Slavery Act Transparency Statement|Sitemap|About US| Contact US: help@patsnap.com