Butenedioic acid resin and preparation method therefor, and degradable micro lubricating oil prepared by using butenedioic acid resin
A technology of butenedioic acid and butenedioic anhydride, which is applied in the field of lubrication, can solve the problems of increasing environmental burden and non-degradable constituent raw materials, and achieves remarkable environmental protection, excellent lubricity and biodegradable performance, and saving usage. Effect
- Summary
- Abstract
- Description
- Claims
- Application Information
AI Technical Summary
Problems solved by technology
Method used
Image
Examples
Embodiment 1
[0037] Step 1, add 116.07kg (1000mol) of fumaric acid and 354.12kg (1900mol) of lauryl alcohol in the polymerization kettle, add 28kg of dilute sulfuric acid (5%), charge into nitrogen to convert the air in the polymerization kettle to react, after the reaction Decompress and discharge water, which is lauryl fumarate.
[0038] Step 2: Add 1.16kg of dibenzoyl peroxide initiator into the polymerization kettle and stir, keep the reaction temperature at 160°C, after 8 hours of polymerization reaction, discharge the polymer in the polymerization kettle, filter and remove it at a temperature above 100°C, etc. Impurities, that is, fumaric acid laurel resin.
[0039] Stir 30kg of the above-mentioned lauryl fumarate, 30kg of trimethylolpropane trioleate, 30kg of methyl oleate, 5kg of trilauryl phosphate, and 5kg of sodium lauryl sarcosinate at a temperature of about 100°C for 20 minutes , which is a degradable micro lubricant, naturally cooled packaging.
Embodiment 2
[0041] Step 1, the maleic acid of 116.07kg (1000mol) and the arachidyl alcohol of 597.1kg (2000mol) are added in the polymerizer, add 71.32kg dilute sulfuric acid (5%), fill into nitrogen and change the air in the polymerizer to react, react After decompression to discharge water, it is peanut ester maleate.
[0042] Step 2: Add 0.58kg of lauroyl peroxide initiator into the polymerization kettle and stir, keep the reaction temperature at 180°C, after 4 hours of polymerization, discharge the polymer in the polymerization kettle, filter and remove other impurities at a temperature above 100°C, It is maleic acid peanut resin.
[0043] Stir 10kg of the above-mentioned peanut ester maleate, 50kg of pentaerythritol tetralaurate, and 40kg of ethyl laurate at a temperature of about 100°C for 20 minutes to obtain a degradable micro-lubricating oil, which is naturally cooled and packaged.
Embodiment 3
[0045] Step 1, the maleic anhydride of 98.02kg (1000mol) and the stearyl alcohol of 527.59kg (1950mol) are added in the polymerizer, add 12.51kg cation exchange resin, charge into nitrogen and change the air in the polymerizer to react, reduce after the reaction Press out the water, which is stearyl maleate.
[0046]Step 2: Add 0.87kg of tert-butyl hydroperoxide to the polymerization kettle and stir, keep the reaction temperature at 170°C, after the polymerization reaction for 6 hours, discharge the polymer in the polymerization kettle, filter and remove impurities such as at a temperature above 100°C, It is stearyl alcohol maleate resin.
[0047] Stir 20kg of stearyl alcohol maleate resin, 40kg of glyceryl tripalmitate, 35kg of methyl palmitate, 2.5kg of trilauryl phosphite, and 2.5kg of myristoyl sarcosine at a temperature of about 100°C for 20 In minutes, it is a degradable micro lubricant, which is naturally cooled and packaged.
PUM
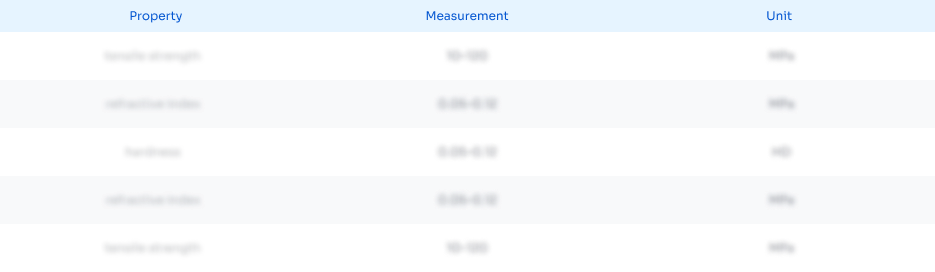
Abstract
Description
Claims
Application Information

- Generate Ideas
- Intellectual Property
- Life Sciences
- Materials
- Tech Scout
- Unparalleled Data Quality
- Higher Quality Content
- 60% Fewer Hallucinations
Browse by: Latest US Patents, China's latest patents, Technical Efficacy Thesaurus, Application Domain, Technology Topic, Popular Technical Reports.
© 2025 PatSnap. All rights reserved.Legal|Privacy policy|Modern Slavery Act Transparency Statement|Sitemap|About US| Contact US: help@patsnap.com