Method for rolling high-precision alloy steel wire rod
A technology for rolling alloy steel rods and wire rods, which is applied in the field of steel rolling, can solve the problems that the dimensional tolerance and ellipticity of finished products cannot be guaranteed, the mechanical properties and dimensional tolerances of special steel products are restricted, and the temperature and rolling control cannot be realized. Improved yield limit, improved mechanical properties, and less modification
- Summary
- Abstract
- Description
- Claims
- Application Information
AI Technical Summary
Problems solved by technology
Method used
Image
Examples
Embodiment 1
[0017] The process of rolling the continuous casting billet with incoming raw material of 150mm×150mm into Φ14mm bar is as follows:
[0018] Step 1: Send the 150mm×150mm billet cold material into the walking heating furnace for heating, the heating temperature is controlled at 950°C, and then transported to six flat vertical roller rough rolling units for rolling to a circular section of Φ71mm, which is the best possible The size closest to the finished product, then fly cut the head and tail;
[0019] Step 2: Send the rough-rolled steel billet obtained in Step 1 into the middle rolling unit of six flat vertical rollers, and roll it into a Φ30mm circular cross section, which is the closest to the size of the finished product, and then fly the shearing head to enter the 1# wear Water cooling device to cool the rolled piece to 850°C;
[0020] Step 3: Send the steel billet obtained in step 2 into six three-roller reducing and sizing units, and roll the billet into a hot circle o...
Embodiment 2
[0023] The process of rolling the continuous casting billet with incoming raw material of 150mm×150mm into Φ15mm bar is as follows:
[0024] Step 1: Send the 150mm×150mm square billet cold material into the walking heating furnace for heating, the heating temperature is controlled at 1000°C, and then transported to six flat vertical roller rough rolling units, and rolled to a circular section of Φ71mm, as far as possible The size closest to the finished product is reached, and then fly-cut head and tail;
[0025] Step 2: Send the rough-rolled steel billet obtained in Step 1 into the middle rolling unit of six flat vertical rollers, and roll it into a Φ30mm circular cross section, which is the closest to the size of the finished product, and then fly the shearing head to enter the 1# wear Water cooling device to cool the rolled piece to 800°C;
[0026] Step 3: Send the steel billet obtained in step 2 into six three-roller sizing units, adjust the opening degree of the rolls on...
Embodiment 3
[0029] The process of rolling the continuous casting billet with incoming raw material of 150mmx150mm into Φ20mm bar is as follows:
[0030] Step 1: Send the 150mm×150mm square billet cold material into the walking heating furnace for heating, the heating temperature is controlled at 1150°C, and then transported to six flat and vertical roll roughing units, rolling to a circular section of Φ71mm, as far as possible The size closest to the finished product is reached, and then fly-cut head and tail;
[0031] Step 2: Send the rough-rolled steel billet obtained in Step 1 into the middle rolling unit of six flat vertical rollers, and roll it into a Φ30mm circular cross section, which is the closest to the size of the finished product, and then fly the shearing head to enter the 1# wear Water cooling device to cool the rolled piece to 830°C;
[0032] Step 3: Send the steel billet obtained in step 2 into six three-roller reducing and sizing units. On the basis of Example 1, it is n...
PUM
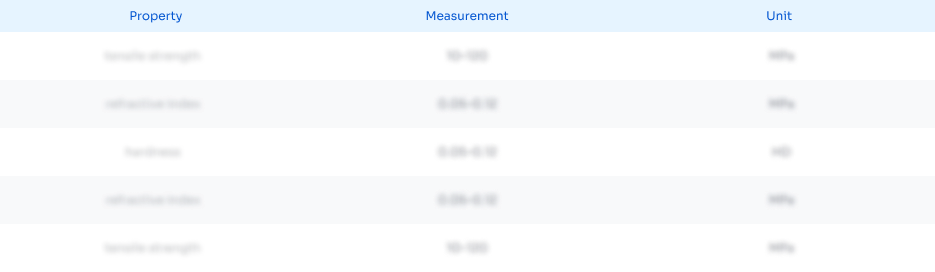
Abstract
Description
Claims
Application Information

- R&D
- Intellectual Property
- Life Sciences
- Materials
- Tech Scout
- Unparalleled Data Quality
- Higher Quality Content
- 60% Fewer Hallucinations
Browse by: Latest US Patents, China's latest patents, Technical Efficacy Thesaurus, Application Domain, Technology Topic, Popular Technical Reports.
© 2025 PatSnap. All rights reserved.Legal|Privacy policy|Modern Slavery Act Transparency Statement|Sitemap|About US| Contact US: help@patsnap.com