Preparation method of wood-plastic material coated with modified nano particle wood powder
A technology of nano-particles and wood-plastic materials, which is applied in the field of preparation of wood-plastic materials, can solve the problems of difficult to reduce the preparation cost, poor mechanical properties of products, complicated processes, etc., and achieves long service life, stable structure and simple preparation method. Effect
- Summary
- Abstract
- Description
- Claims
- Application Information
AI Technical Summary
Problems solved by technology
Method used
Image
Examples
Embodiment 1
[0028] The concrete steps of preparation are:
[0029] Step 1, according to the weight ratio of wood flour:tetraethyl orthosilicate is 2.8:12, add 80 mesh wood flour to the tetraethyl orthosilicate with a temperature of 40°C, a pH value of 2.5, and a concentration of 0.3vol%. Stir in ethyl ester aqueous solution for 2 h; wherein, wood powder is wood powder to obtain a mixed solution. According to the weight ratio of silane coupling agent:tetraethyl orthosilicate as 3:40, add silane coupling agent KH550 dropwise to the mixed solution under stirring after 2h, and react for 0.5h after the dropwise addition to obtain Modified wood flour solution.
[0030] Step 2, the modified wood powder solution is first subjected to suction filtration, ethanol washing and drying, to obtain an approximate figure 1 The modified wood powder shown in c. According to the weight ratio of modified wood flour: polypropylene particles is 35:65, mix the two and place them on the screw extruder, and ext...
Embodiment 2
[0032] The concrete steps of preparation are:
[0033]Step 1, according to the weight ratio of wood flour:tetraethyl orthosilicate of 2.9:11, add 85 mesh wood flour to tetraethyl orthosilicate with a temperature of 43°C, a pH value of 2.8, and a concentration of 0.28vol%. Stir in the ethyl ester aqueous solution for 2.3 h; wherein, the wood powder is wood powder to obtain a mixed solution. According to the weight ratio of silane coupling agent:tetraethyl orthosilicate as 3.5:40, add silane coupling agent KH550 dropwise to the stirred mixed solution after 2h, and react for 0.6h after the dropwise addition to obtain Modified wood flour solution.
[0034] Step 2, the modified wood powder solution is first subjected to suction filtration, ethanol washing and drying, to obtain an approximate figure 1 The modified wood powder shown in c. According to the weight ratio of modified wood flour: polypropylene particles is 38:63, the two are mixed and placed on a screw extruder, and ex...
Embodiment 3
[0036] The concrete steps of preparation are:
[0037] Step 1, according to the weight ratio of wood flour:tetraethyl orthosilicate of 3:10, add 90 mesh wood flour to tetraethyl orthosilicate at a temperature of 45°C, a pH value of 3, and a concentration of 0.25vol%. Stir in the ethyl ester aqueous solution for 2.5 h; wherein, the wood powder is wood powder to obtain a mixed solution. According to the weight ratio of silane coupling agent:tetraethyl orthosilicate of 4:40, add silane coupling agent KH550 dropwise to the mixed solution under stirring after 2h, and react for 0.7h after the dropwise addition to obtain Modified wood flour solution.
[0038] Step 2, the modified wood powder solution is first subjected to suction filtration, ethanol washing and drying to obtain the following: figure 1 The modified wood powder shown in c. According to the weight ratio of modified wood flour: polypropylene particles is 40:60, mix the two and put them on the screw extruder, and extru...
PUM
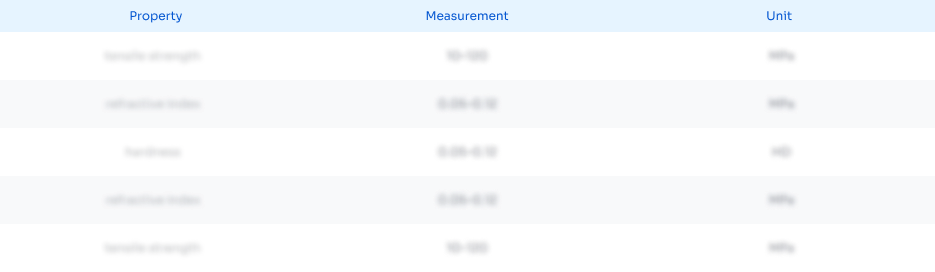
Abstract
Description
Claims
Application Information

- R&D Engineer
- R&D Manager
- IP Professional
- Industry Leading Data Capabilities
- Powerful AI technology
- Patent DNA Extraction
Browse by: Latest US Patents, China's latest patents, Technical Efficacy Thesaurus, Application Domain, Technology Topic, Popular Technical Reports.
© 2024 PatSnap. All rights reserved.Legal|Privacy policy|Modern Slavery Act Transparency Statement|Sitemap|About US| Contact US: help@patsnap.com