A dynamic test method for bridge influence lines
A technology of dynamic testing and influence lines, which is applied in the direction of elastic testing, machine/structural component testing, measuring devices, etc., can solve the problem that the ideal influence line characteristic curve cannot be obtained, and the influence line has amplitude or shape distortion, deviation, etc. question
- Summary
- Abstract
- Description
- Claims
- Application Information
AI Technical Summary
Problems solved by technology
Method used
Image
Examples
Embodiment 1
[0112] Taking a concrete simply supported T-beam bridge with a span of 20.0m as an example, the bridge strain influence line was tested on site and the auxiliary test showed that the vertical vibration frequency of the bridge was 3.06Hz. The direction and position of the vehicle crossing the bridge figure 1 (a), select section 1 at mid-span and section 2 at a distance of 3.1m from the end as the test section; there are 3 effective strain measuring points, and the measuring points are arranged as figure 1 (b), figure 1 As shown in (c), the 3rd beam from left to right at section 1 is measuring point 1, the 2nd beam from left to right at section 2 is measuring point 2, and the first from left to right at section 2 #Beam is measuring point 3. The cross section and measuring points are arranged as figure 1 Shown.
[0113] A three-axle vehicle is used as the test vehicle. The measured 1-2 wheelbase is 4.0m, the 2-3 wheelbase is 1.4m, and the measured three-axle weight is 8.94×10. 3...
Embodiment 2
[0121] From the perspective of model tests, the correctness and feasibility of this method for extracting the influence line of bridges is verified and the advantages of similar methods are compared. The bridge model is a steel girder-slab bridge, which consists of two pieces of 100mm×68mm×4.5mm "I"-shaped steel beams and 4mm thick steel bridge deck welded together, with a length of 5.6m and a width of 0.56m. The vehicle model is a mass-adjustable 2-axle vehicle (wheelbase 0.365m). Its lateral position is constrained by the bridge guide rails. During the test, it is pulled by an electric motor and its speed is controlled. Appropriate approach bridges are installed in front of and behind the bridge to simulate the vehicle’s upper bridge and For bridge exit behavior, the strain measurement points are selected at the bottom of one side steel beam and arranged along the longitudinal direction. The model and measurement points are arranged as Image 6 , Measuring point 1 is arranged ...
PUM
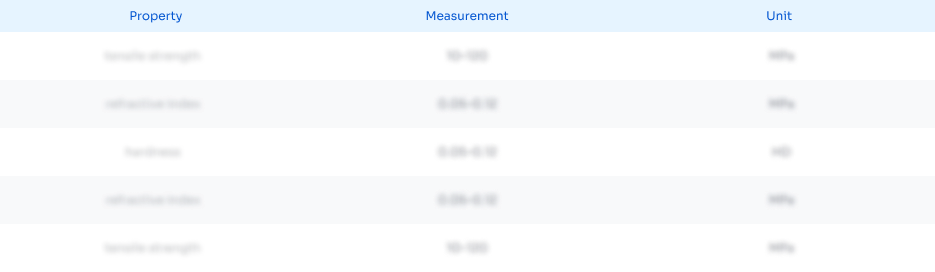
Abstract
Description
Claims
Application Information

- R&D
- Intellectual Property
- Life Sciences
- Materials
- Tech Scout
- Unparalleled Data Quality
- Higher Quality Content
- 60% Fewer Hallucinations
Browse by: Latest US Patents, China's latest patents, Technical Efficacy Thesaurus, Application Domain, Technology Topic, Popular Technical Reports.
© 2025 PatSnap. All rights reserved.Legal|Privacy policy|Modern Slavery Act Transparency Statement|Sitemap|About US| Contact US: help@patsnap.com