Environmentally friendly recovery and treatment method of waste and old lithium iron phosphate power cells
A technology for lithium iron phosphate and power batteries, which is applied in the field of green recycling of waste lithium iron phosphate power batteries, which can solve the problems of serious pollution, complicated process, and high recycling cost of lithium iron phosphate power batteries, and achieve reduced recycling costs and pure powder , excellent performance
- Summary
- Abstract
- Description
- Claims
- Application Information
AI Technical Summary
Problems solved by technology
Method used
Image
Examples
Embodiment 1
[0030] 3 pieces of used 60Ah electric vehicle lithium iron phosphate power batteries were fixed to capacity, discharged at 0.2C, and when the voltage dropped to 0, the batteries were moved to a vacuum glove box, and the batteries were cut and disassembled by mechanical force. Soak the core in NMP solution, dry it after soaking for 6 hours, and directly recover the aluminum-plastic film ( figure 1 B) and tabs ( figure 1 C), while recovering the NMP solution.
[0031] Continue to use mechanical force to separate the cell to obtain the positive electrode sheet, negative electrode sheet and separator, and the separator is directly recycled ( figure 1 A).
[0032] Mechanically pulverize the positive electrode sheet and the negative electrode sheet respectively, and stop when no fragments have a side length greater than 2 cm, soak and stir the fragments in a NaON solution with a pH of 11 for 5 minutes, wash and filter. Dry the obtained material under vacuum condition, collect the...
Embodiment 2
[0038] The steps of Example 2 are basically the same as those of Example 1, except that the sieved positive electrode coarse powder containing lithium iron phosphate and acetylene black is first calcined at 250°C for 5h under nitrogen protection, and then calcined at 300°C for 10h to obtain pure Regenerated lithium iron phosphate positive electrode material; the sieved negative electrode powder containing graphite and acetylene black is calcined at 300°C under air.
[0039] According to the ratio of recovered lithium iron phosphate active material: conductive agent: binder mass ratio of 90:5:5 to make positive electrode sheet, use new graphite negative electrode sheet, diaphragm and electrolyte, in a dry glove box filled with argon The battery was assembled in the medium, and the charge and discharge test was carried out, and the results are shown in Table 1.
[0040] A battery was assembled in a dry glove box filled with argon gas according to the recovered graphite negative ...
Embodiment 3
[0042] The steps of Example 3 are basically the same as in Example 1, except that the sieved positive electrode coarse powder containing lithium iron phosphate and acetylene black is calcined at 250°C for 15h under nitrogen protection to obtain a pure regenerated lithium iron phosphate positive electrode material; The divided negative electrode powder comprising graphite and acetylene black was calcined at 250° C. under air.
[0043] According to the ratio of recovered lithium iron phosphate active material: conductive agent: binder mass ratio of 90:5:5 to make positive electrode sheet, use new graphite negative electrode sheet, diaphragm and electrolyte, in a dry glove box filled with argon The battery was assembled in the medium, and the charge and discharge test was carried out, and the results are shown in Table 1.
[0044] A battery was assembled in a dry glove box filled with argon gas according to the recovered graphite negative electrode material, new lithium iron phos...
PUM
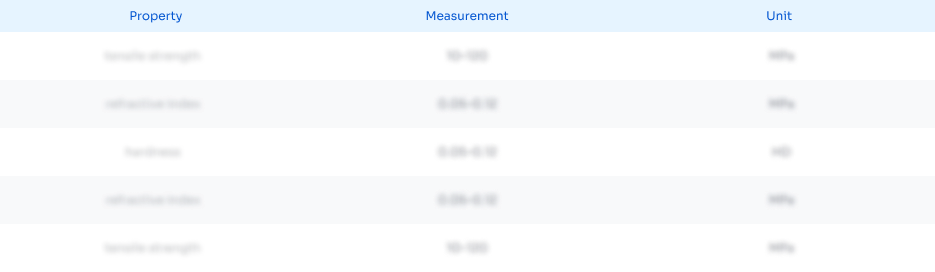
Abstract
Description
Claims
Application Information

- R&D Engineer
- R&D Manager
- IP Professional
- Industry Leading Data Capabilities
- Powerful AI technology
- Patent DNA Extraction
Browse by: Latest US Patents, China's latest patents, Technical Efficacy Thesaurus, Application Domain, Technology Topic, Popular Technical Reports.
© 2024 PatSnap. All rights reserved.Legal|Privacy policy|Modern Slavery Act Transparency Statement|Sitemap|About US| Contact US: help@patsnap.com