A kind of preparation method of high temperature resistant anti-rutting additive
A kind of anti-rutting additive and high-temperature resistance technology, which is used in building thermal insulation materials, building components, buildings, etc., can solve the problems of decreased anti-rutting performance and poor high-temperature resistance, and achieve the effect of improving anti-rutting performance.
- Summary
- Abstract
- Description
- Claims
- Application Information
AI Technical Summary
Problems solved by technology
Method used
Examples
Embodiment 1
[0019] Step 1, preparation of modified epoxy resin: 3-methylcatechol 10Kg, hydroxymalonic acid 4Kg, m-trifluoromethylphenol 12Kg and 4,4'-dihydroxybiphenyl 15Kg with epichlorine Alcohol 90Kg, the aqueous solution of alkali metal hydroxide (sodium hydroxide) is mixed uniformly, and the usage amount of alkali metal hydroxide is 0.8 mole with respect to total hydroxyl amount 1 mole in all monomers, and alkali metal hydroxide The mass concentration of the aqueous solution of the substance is 15wt%, heating reaction, reaction time 1 hour, reaction temperature 50 ℃, after the reaction finishes, evaporate and remove solvent, add benzene or ketone solvent, add water after washing, remove water phase, and organic The phase is evaporated to dryness;
[0020] Step 2, the modified epoxy resin, polyethylene 20Kg, polypropylene 20Kg, crystalline polyester resin 6Kg, styrene-butadiene rubber 9Kg, stearic acid 5Kg, carbon fiber 6Kg, ethyl acetoacetate 10Kg, polyimide fiber 5Kg and 6Kg of eth...
Embodiment 2
[0022] Step 1, preparation of modified epoxy resin: mix 20Kg of 3-methylcatechol, 6Kg of hydroxymalonic acid, 16Kg of m-trifluoromethylphenol and 30Kg of 4,4'-dihydroxybiphenyl with epichlorine Alcohol 140Kg, the aqueous solution of alkali metal hydroxide (sodium hydroxide) is mixed uniformly, and the usage amount of alkali metal hydroxide is 1.2 moles relative to the total hydroxyl amount in all monomers, and alkali metal hydroxide The mass concentration of the aqueous solution of the compound is 20wt%, heating reaction, reaction time 10 hours, reaction temperature 90 ℃, after reaction finishes, evaporate and remove solvent, add benzene or ketone solvent, add water after washing again, remove water phase, organic The phase is evaporated to dryness;
[0023] Step 2, the modified epoxy resin, polyethylene 30Kg, polypropylene 30Kg, crystalline polyester resin 12Kg, styrene-butadiene rubber 15Kg, stearic acid 10Kg, carbon fiber 12Kg, ethyl acetoacetate 15Kg, polyimide fiber 10Kg...
Embodiment 3
[0025] Step 1, preparation of modified epoxy resin: mix 3-methylcatechol 15Kg, hydroxymalonic acid 5Kg, m-trifluoromethylphenol 15Kg and 4,4'-dihydroxybiphenyl 20Kg with epichlorine 130Kg of alcohol and an aqueous solution of alkali metal hydroxide (sodium hydroxide) are mixed evenly. The amount of alkali metal hydroxide used is 1.1 moles relative to the total hydroxyl group in all monomers. The amount of alkali metal hydroxide The mass concentration of the aqueous solution is 17wt%. Heating the reaction, the reaction time is 5 hours, and the reaction temperature is 70°C. After the reaction, evaporate the solvent, add benzene or ketone solvent, add water to wash, remove the water phase, and evaporate the organic phase. get it dry;
[0026] Step 2, the modified epoxy resin, polyethylene 25Kg, polypropylene 25Kg, crystalline polyester resin 10Kg, styrene-butadiene rubber 12Kg, stearic acid 8Kg, carbon fiber 11Kg, ethyl acetoacetate 12Kg, polyimide fiber 7Kg and 8Kg of ethylene-...
PUM
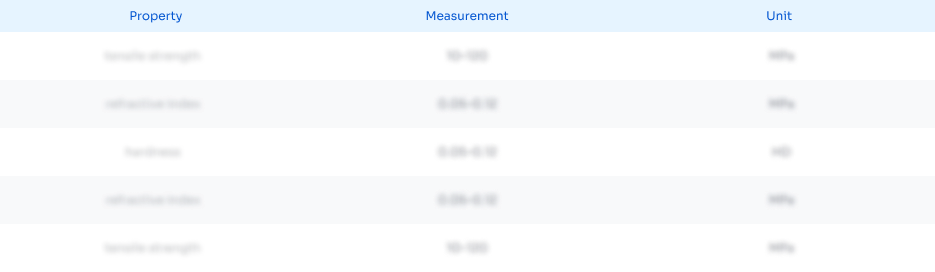
Abstract
Description
Claims
Application Information

- R&D
- Intellectual Property
- Life Sciences
- Materials
- Tech Scout
- Unparalleled Data Quality
- Higher Quality Content
- 60% Fewer Hallucinations
Browse by: Latest US Patents, China's latest patents, Technical Efficacy Thesaurus, Application Domain, Technology Topic, Popular Technical Reports.
© 2025 PatSnap. All rights reserved.Legal|Privacy policy|Modern Slavery Act Transparency Statement|Sitemap|About US| Contact US: help@patsnap.com