Ammonia spraying amount controlling method for SNCR (selective no catalytic reduction) flue gas denitrating system for cement manufacturing
A control method and ammonia injection rate technology, applied in the field of flue gas denitrification, can solve the problems of difficult real-time and accurate control of ammonia injection rate, and difficulty in overcoming system nonlinearity and hysteresis, so as to be easy to popularize and use, improve NOx removal rate, and realize The effect of meeting emission standards
- Summary
- Abstract
- Description
- Claims
- Application Information
AI Technical Summary
Problems solved by technology
Method used
Image
Examples
Embodiment 1
[0024] Embodiment 1: Construction and training of BP neural network prediction model for ammonia injection amount
[0025] ① Construction of BP neural network prediction model for ammonia injection amount
[0026] In this embodiment, the ammonia injection amount BP neural network forecasting model is made up of input layer, hidden layer and output layer, such as figure 2 shown. Set the input layer neurons to Q(t), X in (t), T(t), X out (t+1) and U(t+1), where Q(t) is the inlet flue gas flow rate of the cement kiln calciner at time t, X in (t) is NO in flue gas at the inlet of cement kiln calciner at time t x concentration, T(t) is the inlet flue gas temperature of the cement kiln calciner at time t, X out (t+1) is the NO in the outlet flue gas of the cement kiln calciner at the moment (t+1) x concentration, U(t+1) is the NH in the outlet flue gas of the cement kiln calciner at time (t+1) 3 concentration; set the output layer neurons to y(t) and y 1 (t) / y 2 (t), where...
Embodiment 2
[0054] Example 2: Ammonia injection control of SNCR flue gas denitrification system in cement production
[0055] For the device configuration of this embodiment, see figure 1 , set two layers of ammonia injection areas in the 850-1050 °C area of the cement kiln calciner 1, the first layer of ammonia injection area 2 is set at 900-1050 °C in the cement kiln calciner, and the second layer of ammonia injection area 3 is set at At 850-960°C of the cement kiln decomposition furnace, the first layer of ammonia injection zone and the second layer of ammonia injection zone are equipped with corresponding spray guns 15, and the spray guns 15 of the first layer of ammonia injection zone and the second layer of ammonia spray zone are respectively controlled by the first layer of ammonia injection zone. Ammonia flow regulating valve 4 in the ammonia injection zone on the first floor and ammonia flow regulating valve 5 in the ammonia spraying zone on the second floor control the amount ...
PUM
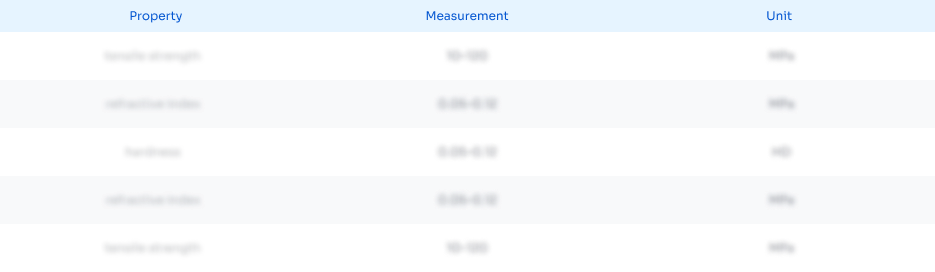
Abstract
Description
Claims
Application Information

- R&D Engineer
- R&D Manager
- IP Professional
- Industry Leading Data Capabilities
- Powerful AI technology
- Patent DNA Extraction
Browse by: Latest US Patents, China's latest patents, Technical Efficacy Thesaurus, Application Domain, Technology Topic, Popular Technical Reports.
© 2024 PatSnap. All rights reserved.Legal|Privacy policy|Modern Slavery Act Transparency Statement|Sitemap|About US| Contact US: help@patsnap.com