A Mechanism Test Method for Fatigue Crack Growth Based on Small Time Scale
A fatigue crack propagation, small time scale technology, applied in the direction of applying repetitive force/pulsation force to test the strength of materials, etc., can solve the problems of large analysis time scale, neglect of metallographic corrosion, low accuracy, etc., to achieve the effect of improving analysis accuracy
- Summary
- Abstract
- Description
- Claims
- Application Information
AI Technical Summary
Problems solved by technology
Method used
Image
Examples
Embodiment Construction
[0027] The method of the present invention will be described in detail below in conjunction with the accompanying drawings.
[0028] (1) Prepare plane stress specimens.
[0029] According to the requirements of the in-situ stretching table equipped with the scanning electron microscope, the in-situ crack growth specimens in the plane stress state were prepared, such as figure 1 As shown; 0.2mm diameter molybdenum wire was used for wire cutting to prefabricate the sample gap; all samples were numbered.
[0030] (2) Metallographic structure analysis and calibration.
[0031] The surface of the sample is roughly ground, using metallographic sandpaper with a particle size of 400, 600 and 800, and the sample is roughly ground from coarse to fine. Every time the No. 1 sandpaper is replaced, the grinding surface of the sample must be turned 90 degrees until the surface is clear Scratches appear; the surface of the sample is finely ground, and the sample is finely ground with 1500, ...
PUM
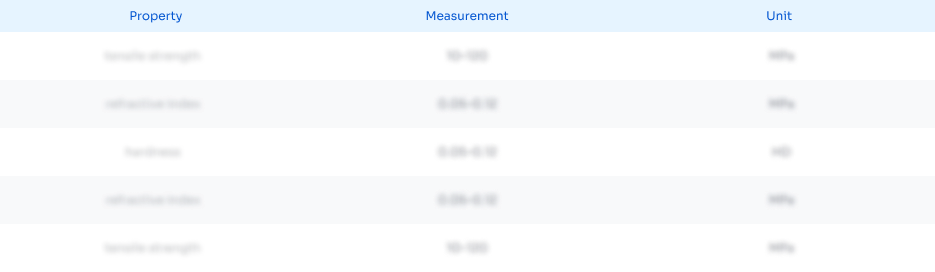
Abstract
Description
Claims
Application Information

- R&D
- Intellectual Property
- Life Sciences
- Materials
- Tech Scout
- Unparalleled Data Quality
- Higher Quality Content
- 60% Fewer Hallucinations
Browse by: Latest US Patents, China's latest patents, Technical Efficacy Thesaurus, Application Domain, Technology Topic, Popular Technical Reports.
© 2025 PatSnap. All rights reserved.Legal|Privacy policy|Modern Slavery Act Transparency Statement|Sitemap|About US| Contact US: help@patsnap.com