Method for softening and rolling cold forging steel
A cold heading steel and steel coil technology, applied in the field of steel pressure processing, can solve the problems of high difficulty in rolling, high consumption of spare parts, high difficulty, etc., and achieve the effect of improving deep processing capacity, simple rolling process, and improving production efficiency
- Summary
- Abstract
- Description
- Claims
- Application Information
AI Technical Summary
Problems solved by technology
Method used
Image
Examples
Embodiment 1
[0036] Embodiment 1: Comparative test of softening and rolling of cold heading steel
[0037] Three steel grades, 10B21, ML20MnTiB, and ML 35CrMo, were selected as test materials, and the rolling specifications were 12, 16, and 20 mm, respectively. The furnace batches of each steel type are the same, and then they are divided into a test group and a control group, and the production quantity of each group is 10 groups of wire rods. All wire rods are produced on the same high-speed wire rod production line. The production method of the control group adopts the conventional production process, that is, the heating temperature is 1120-1170 °C, the starting rolling temperature is 950-985 °C, and the finishing rolling temperature is 850-870 °C. The silk temperature is 820~860°C, the fan and heat preservation cover on the Stelmo roller table are all closed, the conveying speed of the first section is 0.20~0.30m / s, the conveying speed of the final section is 0.30~0.40m / s, the coil co...
Embodiment 2
[0042] Embodiment 2: Steel process performance index test
[0043] By measuring the mechanical indexes of the steel, the process performance of the cold heading steel in the control group and the test group in Example 1 was compared. The results are shown in Table 2, and the data in the table are the average values of 10 groups of wire rods in the control group and the test group.
[0044] Table 2 Test results of steel process performance indicators
[0045]
[0046] *Note: Sectional shrinkage increase = shrinkage rate of test group - shrinkage rate of control group
[0047] It can be seen from Table 2 that the softening effect of the cold heading steel produced by the method of the present invention is remarkable. In addition, after the mass production of the product, it has been used by downstream users to completely realize the production of standard parts of all levels without annealing, which effectively reduces the production cost. The invention conforms to the i...
PUM
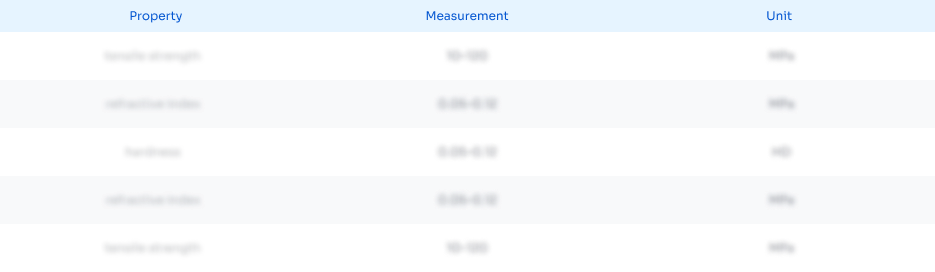
Abstract
Description
Claims
Application Information

- R&D Engineer
- R&D Manager
- IP Professional
- Industry Leading Data Capabilities
- Powerful AI technology
- Patent DNA Extraction
Browse by: Latest US Patents, China's latest patents, Technical Efficacy Thesaurus, Application Domain, Technology Topic, Popular Technical Reports.
© 2024 PatSnap. All rights reserved.Legal|Privacy policy|Modern Slavery Act Transparency Statement|Sitemap|About US| Contact US: help@patsnap.com