Preparation method of novel low-noise EVA (ethylene vinyl acetate copolymer) cable material
A low-noise, cable material technology, used in circuits, electrical components, plastic/resin/wax insulators, etc., can solve problems such as poor anti-noise performance, inability to use low-noise cables, and limited application scope, to improve anti-noise performance. , the effect of reducing noise value and improving compatibility
- Summary
- Abstract
- Description
- Claims
- Application Information
AI Technical Summary
Problems solved by technology
Method used
Image
Examples
Embodiment 1
[0025] A new type of low-noise EVA cable material preparation method, the steps are as follows:
[0026] (1) Crush the natural coral with a pulverizer and add it to a 10% sodium hydroxide solution, soak for 2 hours and then move it to an acetone solution for ultrasonic cleaning for 30 minutes, take it out, and dry it at 80°C for 3 hours to obtain coral powder ;
[0027] (2) Ball mill the coral powder obtained in step (1) with a ball mill for 10 hours, add it to a 40% ethanol solution and stir and mix to form a suspension, add polyethylene glycol to the suspension and magnetically stir for 2 hours, then discharge Then it was placed in a vacuum drying oven at 90°C and vacuum dried for 10 hours, taken out, ground, and passed through a 300-mesh sieve to obtain modified coral powder. The weight ratio of coral powder, ethanol solution and polyethylene glycol was 48:48: 1;
[0028] (3) Add the nano boron fiber to the toluene solution and soak for 48 hours, place it in a drying oven to dry...
Embodiment 2
[0031] A new type of low-noise EVA cable material preparation method, its steps are as follows:
[0032] (1) Crush the natural coral with a pulverizer and add it to a 10% sodium hydroxide solution, soak for 2 hours and then move it to an acetone solution for ultrasonic cleaning for 30 minutes, take it out, and dry it at 80°C for 3 hours to obtain coral powder ;
[0033] (2) Ball mill the coral powder obtained in step (1) with a ball mill for 10 hours, add it to a 40% ethanol solution and stir and mix to form a suspension, add polyethylene glycol to the suspension and magnetically stir for 2 hours, discharge After that, it was placed in a vacuum drying box for vacuum drying at 90°C for 10 hours, taken out, ground, and passed through a 300-mesh sieve to obtain modified coral powder. The weight ratio of coral powder, ethanol solution, and polyethylene glycol was 48:48: 1;
[0034] (3) Add the nano boron fiber to the toluene solution and soak for 48 hours, put it in a drying oven to dr...
Embodiment 3
[0037] A new type of low-noise EVA cable material preparation method, its steps are as follows:
[0038] (1) Crush the natural coral with a pulverizer and add it to a 10% sodium hydroxide solution, soak for 2 hours and then move it to an acetone solution for ultrasonic cleaning for 30 minutes, take it out, and dry it at 80°C for 3 hours to obtain coral powder ;
[0039] (2) Ball mill the coral powder obtained in step (1) with a ball mill for 10 hours, add it to a 40% ethanol solution and stir and mix to form a suspension, add polyethylene glycol to the suspension and magnetically stir for 2 hours, discharge After that, it was placed in a vacuum drying box for vacuum drying at 90°C for 10 hours, taken out, ground, and passed through a 300-mesh sieve to obtain modified coral powder. The weight ratio of coral powder, ethanol solution, and polyethylene glycol was 48:48: 1;
[0040] (3) Add the nano boron fiber to the toluene solution and soak for 48 hours, place it in a drying oven to ...
PUM
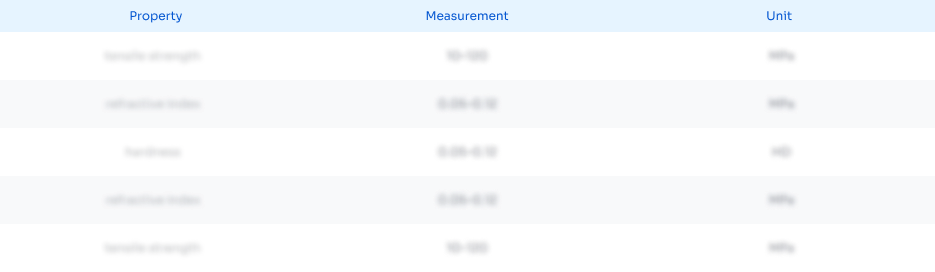
Abstract
Description
Claims
Application Information

- R&D Engineer
- R&D Manager
- IP Professional
- Industry Leading Data Capabilities
- Powerful AI technology
- Patent DNA Extraction
Browse by: Latest US Patents, China's latest patents, Technical Efficacy Thesaurus, Application Domain, Technology Topic, Popular Technical Reports.
© 2024 PatSnap. All rights reserved.Legal|Privacy policy|Modern Slavery Act Transparency Statement|Sitemap|About US| Contact US: help@patsnap.com