Method for improving content of vanadium pentoxide in vanadium slag
A vanadium pentoxide and vanadium slag technology, applied in the direction of manufacturing converters, can solve problems such as sticking to the kiln, and achieve the effects of reducing vanadium slag crushing, reducing energy consumption and improving production efficiency
- Summary
- Abstract
- Description
- Claims
- Application Information
AI Technical Summary
Problems solved by technology
Method used
Image
Examples
Embodiment 1
[0014] The composition of molten iron is:
[0015]
[0016] (1) Vanadium extraction: Blowing oxygen into the molten iron by blowing top and bottom, and the oxygen supply pressure is controlled at 0.8MPa;
[0017] (2) Oxygen blowing oxidation of vanadium slag: After pouring out the semi-steel, continue to carry out oxygen blowing oxidation on the vanadium slag, adopt the top-bottom double blowing method to blow oxygen, the oxygen pressure is controlled at 0.3MPa, the gun position is controlled at 680mm, and the oxidation temperature is 900°C. V in slag before oxygen blowing 5+ / TV is 0.11, the V in the slag after oxygen blowing ends 5+ / TV is 0.90.
Embodiment 2
[0019] The composition of molten iron is:
[0020]
[0021] (1) Vanadium extraction: Oxygen is blown into the molten iron by top-bottom double-blowing, and the oxygen supply pressure is controlled at 0.75MPa;
[0022] (2) Oxygen blowing oxidation of vanadium slag: After pouring out the semi-steel, continue to carry out oxygen blowing oxidation on the vanadium slag, adopt the top-bottom double blowing method to blow oxygen, the oxygen pressure is controlled at 0.2MPa, the gun position is controlled at 600mm, and the oxidation temperature is 1000℃, V in slag before oxygen blowing 5+ / TV is 0.08, the V in the slag after oxygen blowing 5+ / TV is 0.87
Embodiment 3
[0024] The composition of molten iron is:
[0025]
[0026] (1) Vanadium extraction: Blow oxygen into the molten iron by top blowing, and the oxygen supply pressure is controlled at 0.6MPa;
[0027] (2) Oxygen blowing oxidation of vanadium slag: After the semi-steel is poured out, continue to carry out oxygen blowing oxidation on the vanadium slag, using the top blowing method to blow oxygen, the oxygen pressure is controlled at 0.1MPa, the gun position is controlled at 400mm, and the oxidation temperature is 800°C , V in the slag before oxygen blowing 5+ / TV is 0.12, the V in the slag after oxygen blowing ends 5+ / TV is 0.93.
PUM
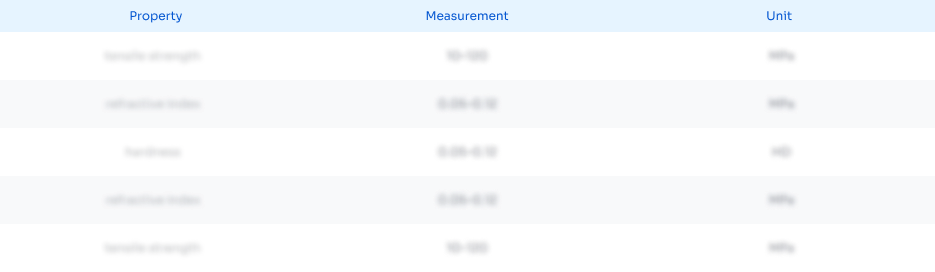
Abstract
Description
Claims
Application Information

- R&D
- Intellectual Property
- Life Sciences
- Materials
- Tech Scout
- Unparalleled Data Quality
- Higher Quality Content
- 60% Fewer Hallucinations
Browse by: Latest US Patents, China's latest patents, Technical Efficacy Thesaurus, Application Domain, Technology Topic, Popular Technical Reports.
© 2025 PatSnap. All rights reserved.Legal|Privacy policy|Modern Slavery Act Transparency Statement|Sitemap|About US| Contact US: help@patsnap.com