180-grade straight welded polyurethane wire enamel and preparation method thereof
A technology of polyurethane varnish and wire varnish, which is applied in the field of enamelled wire varnish and its preparation, can solve the problems of high raw material price, low inflection point temperature of dielectric loss curve, and low soft armor breakdown temperature, etc. Excellent effect of softening breakdown temperature and inflection point temperature of dielectric loss curve, thermal shock performance and salt water pinhole performance
- Summary
- Abstract
- Description
- Claims
- Application Information
AI Technical Summary
Problems solved by technology
Method used
Examples
Embodiment 1
[0032] (1) Preparation of polyester polyol resin:
[0033] 873.8 grams of dimethyl terephthalate, 248.3 grams of ethylene glycol, 180 grams of 1,4-butanediol, 104.2 grams of neopentyl glycol, 184.2 grams of glycerol, 136.2 grams of pentaerythritol, and 8.6 grams of zinc acetate were added to the reaction Stir and heat up to dissolve and react, and control the temperature at the top of the kettle to not be higher than 70°C; when the amount of methanol produced reaches 288 grams, lower the temperature of the system to 150°C.
[0034] Then add 296.2 grams of phthalic anhydride, 218.1 grams of pyromellitic anhydride, and 192.1 grams of trimellitic anhydride, heat up to continue the reaction, and control the temperature at the top of the kettle to be no higher than 100°C; when the water output reaches 108 grams, reduce the system temperature to 150 ℃, add the mixed solvent of 2135.0 gram m-p-cresol and xylene to obtain polyester polyol resin, wherein the mass ratio of m-p-cresol an...
Embodiment 2
[0046] (1) Preparation of polyester polyol resin:
[0047] 582.5 grams of dimethyl terephthalate, 372.4 grams of ethylene glycol, 360.5 grams of 1,4-butanediol, 104.2 grams of neopentyl glycol, 184.2 grams of glycerol, 136.2 grams of pentaerythritol, and 8.7 grams of zinc acetate were added to the reaction Stir and heat up to dissolve and react, and control the temperature at the top of the kettle to not be higher than 70°C; when the amount of methanol produced reaches 192 grams, lower the temperature of the system to 150°C.
[0048] Then add 444.3 grams of phthalic anhydride, 327.2 grams of pyromellitic anhydride, and 146.1 grams of adipic acid, and continue the reaction by raising the temperature, controlling the temperature at the top of the kettle to not be higher than 100°C; To 150 DEG C, add 2321.0 g of m-p-cresol and xylene as a mixed solvent to obtain a polyester polyol resin, wherein the mass ratio of m-p-cresol to xylene is 1:1.
[0049] In the above formula, the ra...
PUM
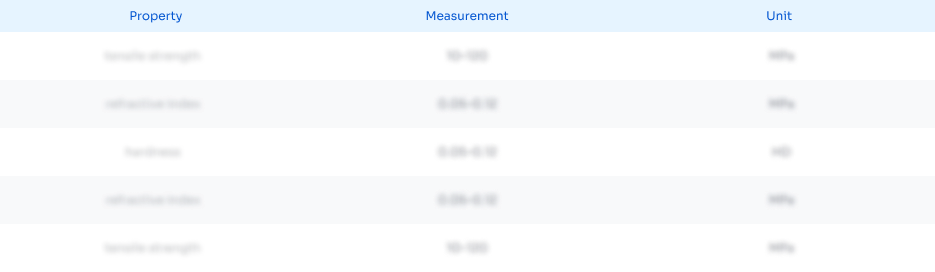
Abstract
Description
Claims
Application Information

- R&D
- Intellectual Property
- Life Sciences
- Materials
- Tech Scout
- Unparalleled Data Quality
- Higher Quality Content
- 60% Fewer Hallucinations
Browse by: Latest US Patents, China's latest patents, Technical Efficacy Thesaurus, Application Domain, Technology Topic, Popular Technical Reports.
© 2025 PatSnap. All rights reserved.Legal|Privacy policy|Modern Slavery Act Transparency Statement|Sitemap|About US| Contact US: help@patsnap.com