Vanadium tailings large-scale utilization and production method
A technology for extracting vanadium tailings and production methods, applied in furnaces, blast furnace details, blast furnaces, etc., can solve problems such as difficult production lines, and achieve the effects of increasing sintering yield, increasing accuracy, and improving mineral phase structure
- Summary
- Abstract
- Description
- Claims
- Application Information
AI Technical Summary
Problems solved by technology
Method used
Image
Examples
Embodiment 1
[0039] 63.4% Baima concentrate, 11% mixed powder, 6.1% medium powder and 5% vanadium extraction tailings are used as iron-containing raw materials, the amount of gas ash is 3%, the amount of limestone is 6.7%, the amount of active ash is 4%, coke powder The dosage is 3%, the dosage of anthracite is 1.8%, the alkalinity of the mixture is 1.85, and the external sinter is 26%, then mixed and granulated to obtain the mixture, which is distributed on the belt sintering machine, ignited and sintered to obtain the finished sinter . The obtained vertical sintering speed is 17.25mm / min, the utilization coefficient is 1.43t / (m2·h1), the yield is 83.15%, and the drum index is 57.73%.
Embodiment 2
[0041]With 63.1% Baima concentrate, 11.5% mixed powder, 5.7% medium powder and 6.5% vanadium extraction tailings as iron-containing raw materials, the amount of gas ash is 3%, the amount of limestone is 6.6%, the amount of active ash is 4%, coke powder The dosage is 3%, the dosage of anthracite is 1.8%, the alkalinity of the mixture is 1.85, and the external sinter is 24.8%, then mixed and granulated to obtain the mixture, which is distributed on the belt sintering machine, ignited and sintered to obtain the finished sinter . The obtained vertical sintering speed is 17.66mm / min, the utilization coefficient is 1.45t / (m2·h1), the yield is 83.55%, and the drum index is 57.27%.
Embodiment 3
[0043] 62.7% Baima concentrate, 12% mixed powder, 5.3% medium powder and 8.5% vanadium extraction tailings are used as iron-containing raw materials, the amount of gas ash is 3%, the amount of limestone is 6.5%, the amount of active ash is 4%, coke powder The dosage is 3%, the dosage of anthracite is 1.8%, the alkalinity of the mixture is 1.85, and the external sinter is 23.2%, and then mixed and granulated to obtain the mixture, which is distributed on the belt sintering machine, ignited and sintered to obtain the finished sinter . The obtained vertical sintering speed is 18.95mm / min, the utilization coefficient is 1.59t / (m2·h1), the yield is 84.47%, and the drum index is 56.93%.
PUM
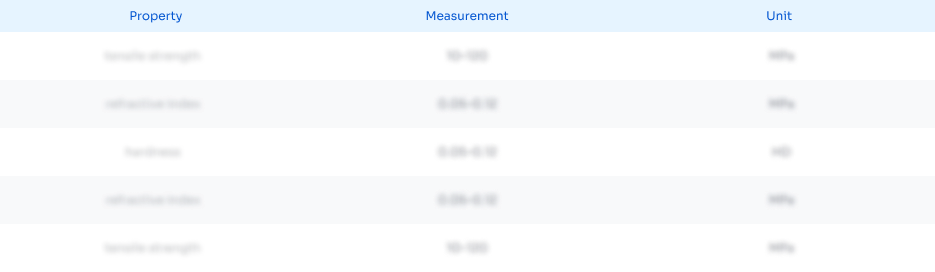
Abstract
Description
Claims
Application Information

- R&D Engineer
- R&D Manager
- IP Professional
- Industry Leading Data Capabilities
- Powerful AI technology
- Patent DNA Extraction
Browse by: Latest US Patents, China's latest patents, Technical Efficacy Thesaurus, Application Domain, Technology Topic, Popular Technical Reports.
© 2024 PatSnap. All rights reserved.Legal|Privacy policy|Modern Slavery Act Transparency Statement|Sitemap|About US| Contact US: help@patsnap.com