Glass wool ceiling board and preparation method thereof
A glass wool board and ceiling technology, applied in glass manufacturing equipment, chemical instruments and methods, glass/slag layered products, etc., can solve the problem that the appearance cannot meet the rich and diverse market needs, it is not easy to carry and install, and safety hazards, etc. Problems, to achieve the effect of rich and diverse shapes, easy handling and installation, and good thermal insulation effect
- Summary
- Abstract
- Description
- Claims
- Application Information
AI Technical Summary
Problems solved by technology
Method used
Examples
Embodiment 1
[0035] A kind of glass wool ceiling, it comprises glass wool board layer, glass fiber felt layer, gypsum paint layer, described glass wool board layer is made by the centrifugal glass wool fiber that environmental protection resin binder is evenly distributed on the surface, described centrifugal The mass ratio of glass wool fiber to environmental protection resin binder and gypsum coating is: 85:7:2, and the described environmental protection resin binder is made up of environmental protection resin and additive and their mass ratio is 2:1, and described The environmental protection resin is common acrylic resin or thermosetting acrylic resin, and the additives are composed of silicone oil, silane and soft water, and their mass ratio is 3:0.2:500.
[0036] A kind of preparation method of above-mentioned glass wool ceiling, it comprises the following steps:
[0037] A. First add 400 parts by weight of environmentally friendly resin and 200 parts of additives into the mixing ta...
Embodiment 2
[0042]A kind of glass wool ceiling, it comprises glass wool board layer, glass fiber felt layer, gypsum paint layer, described glass wool board layer is made by the centrifugal glass wool fiber that environmental protection resin binder is evenly distributed on the surface, described centrifugal The mass ratio of glass wool fiber to environmental protection resin binder and gypsum coating is: 93:15:3, and described environmental protection resin binder is made up of environmental protection resin and additive and their mass ratio is 8:5, and described The environmental protection resin is common acrylic resin or thermosetting acrylic resin, and the additives are composed of silicone oil, silane and soft water with a mass ratio of 8:1.5:700.
[0043] A kind of preparation method of above-mentioned glass wool ceiling, it comprises the following steps:
[0044] A. First add 480 parts by weight of environmentally friendly resin and 300 parts of additives into the mixing tank and s...
Embodiment 3
[0049] A kind of glass wool ceiling, it comprises glass wool board layer, glass fiber felt layer, gypsum paint layer, described glass wool board layer is made by the centrifugal glass wool fiber that environmental protection resin binder is evenly distributed on the surface, described centrifugal The mass ratio of glass wool fiber to environmental protection resin binder and plaster coating is: 89:11:2.5, and described environmental protection resin binder is made up of environmental protection resin and additive and their mass ratio is 44:25, and described The environmental protection resin is common acrylic resin or thermosetting acrylic resin, and the additives are composed of silicone oil, silane and soft water with a mass ratio of 5.5:0.8:600.
[0050] A kind of preparation method of above-mentioned glass wool ceiling, it comprises the following steps:
[0051] A. First, add 440 parts by weight of environmentally friendly resin and 250 parts of additives into the mixing t...
PUM
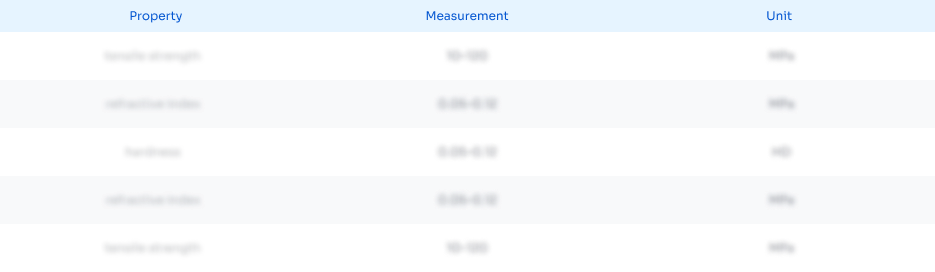
Abstract
Description
Claims
Application Information

- R&D
- Intellectual Property
- Life Sciences
- Materials
- Tech Scout
- Unparalleled Data Quality
- Higher Quality Content
- 60% Fewer Hallucinations
Browse by: Latest US Patents, China's latest patents, Technical Efficacy Thesaurus, Application Domain, Technology Topic, Popular Technical Reports.
© 2025 PatSnap. All rights reserved.Legal|Privacy policy|Modern Slavery Act Transparency Statement|Sitemap|About US| Contact US: help@patsnap.com