Method for preparing sintered ore by utilizing high silicon powder ore
A technology of sinter and fine ore, which is applied in the field of preparing sinter ore by using high-silica powder ore, can solve the problems of influence, unfavorable fluidity of blast furnace slag, etc., and achieve the effect of reducing the cost of batching
- Summary
- Abstract
- Description
- Claims
- Application Information
AI Technical Summary
Problems solved by technology
Method used
Image
Examples
Embodiment Construction
[0016] The above-mentioned and other technical features and advantages of the present invention will be described in more detail below in conjunction with the embodiments.
[0017] The concrete flow process of the method for preparing sintered ore by utilizing high silica fume ore of the present invention is as follows:
[0018] Step S1: Ingredients are prepared according to the following mass percentages:
[0019] Iron concentrate A9%-12%, iron concentrate B9%-12%, low silica fume ore 23%-30%, high silica fume ore 2%-9%, limestone 4.5%-9.0%, serpentine 0% -2.0%, dolomite 0%-4%, quicklime 2.5%-3.5%, coke powder 4.0%-4.5%, return ore 28%-35%;
[0020] The iron concentrate A includes the following components in mass percentage: TFe 65.30-67.50%, FeO 27.50-30.20%, CaO 1.25-1.80%, SiO 2 0.90~1.23%, MgO 0.68~1.15%, F 0.23~0.40%, P 0~0.10%, S 0.625~1.120%, K 2 O 0.095~0.150%, Na 2 O 0.050~0.095% and Al 2 o 3 0.132-0.180%, and the burning loss of the iron concentrate A is 1.35-...
PUM
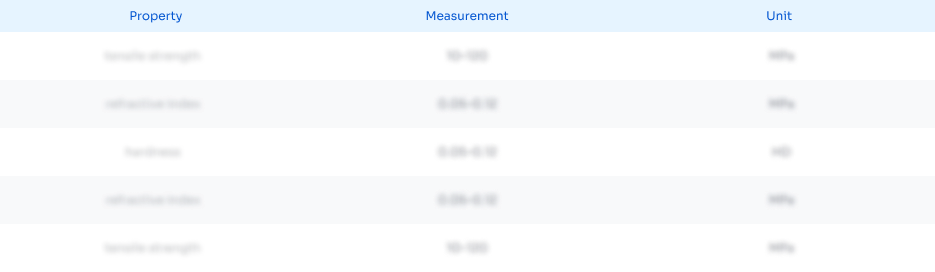
Abstract
Description
Claims
Application Information

- Generate Ideas
- Intellectual Property
- Life Sciences
- Materials
- Tech Scout
- Unparalleled Data Quality
- Higher Quality Content
- 60% Fewer Hallucinations
Browse by: Latest US Patents, China's latest patents, Technical Efficacy Thesaurus, Application Domain, Technology Topic, Popular Technical Reports.
© 2025 PatSnap. All rights reserved.Legal|Privacy policy|Modern Slavery Act Transparency Statement|Sitemap|About US| Contact US: help@patsnap.com