Grinding method of water-quenched carbide slag
A technology of carbide slag and water quenching, which is applied in the field of powder processing, can solve the problems of low grinding efficiency, non-conforming particle size, and large loss of steel balls, so as to save consumption, uniform and stable powder particle size, and reduce unit electricity. consumption effect
- Summary
- Abstract
- Description
- Claims
- Application Information
AI Technical Summary
Problems solved by technology
Method used
Image
Examples
Embodiment Construction
[0012] The present invention will be further described below in conjunction with specific embodiments.
[0013] The invention is a method for grinding water quenched carbonized slag. The water quenched carbonized slag is directly added to the silo of a ball mill, and the carbonized slag powder is directly prepared by grinding in a silo; the grinding body in the silo Are steel balls with two different particle sizes, the diameter of the two steel balls is Two unequal values between the two, and the difference between the diameters of the two steel balls is not less than 20mm, for example, the diameter of the small grain steel ball is Then the diameter of the large grain steel ball is Any value in; for example, the diameter of a large grain steel ball is Then the diameter of the small grain steel ball is Any value in; the weight of the small-sized steel ball is 60%-75% of the weight of the grinding body, and the rest is the large-sized steel ball; the filling rate of the steel...
PUM
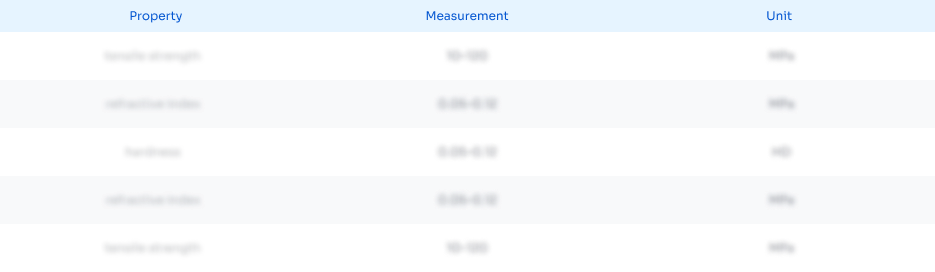
Abstract
Description
Claims
Application Information

- R&D
- Intellectual Property
- Life Sciences
- Materials
- Tech Scout
- Unparalleled Data Quality
- Higher Quality Content
- 60% Fewer Hallucinations
Browse by: Latest US Patents, China's latest patents, Technical Efficacy Thesaurus, Application Domain, Technology Topic, Popular Technical Reports.
© 2025 PatSnap. All rights reserved.Legal|Privacy policy|Modern Slavery Act Transparency Statement|Sitemap|About US| Contact US: help@patsnap.com