Zn/ZSM-11 molecular sieve catalyst modification method
A technology of ZSM-11 and molecular sieve, which is applied in molecular sieve catalysts, physical/chemical process catalysts, chemical instruments and methods, etc., can solve the problems of catalyst skeleton dealumination, overheating, high energy consumption, etc., and achieve the effect of increasing the yield of aromatics
- Summary
- Abstract
- Description
- Claims
- Application Information
AI Technical Summary
Problems solved by technology
Method used
Image
Examples
Embodiment 1
[0026] Put 20g of Na-type ZSM-11 molecular sieve in 100ml of sodium hydroxide with a concentration of 0.3mol / L and a mixed solution of CTAB with a concentration of 0.1mol / L, heat treatment in a water bath at 75°C for 3 hours, filter and wash to medium Drying at 110°C for 3 hours, calcination at 540°C for 3 hours. The prepared molecular sieve was exchanged with 0.8mol / L ammonium nitrate solution three times (1 hour / time), washed with water three times (1 hour / time), dried at 110°C for 10 hours, roasted at 540°C for 4 hours, and then used with an equal volume of Catalyst Cat-C was prepared by impregnation method with zinc metal loaded at 4.0wt%, dried at 110°C for 10 hours, and calcined at 540°C for 4 hours. Wherein ammonium nitrate exchange and water washing temperature is 85 ℃. Gained catalyst detects through XRF, and the Na in this catalyst 2 O is less than 0.05 wt%.
Embodiment 2
[0028] Put 20g of Na-type ZSM-11 molecular sieve in 100ml of sodium hydroxide with a concentration of 0.4mol / L and a mixed solution of PDADMAC with a concentration of 0.1mol / L, heat it in a water bath at 80°C for 2 hours, filter and wash to medium Properties, drying at 100°C for 6 hours, calcination at 580°C for 3 hours. The prepared molecular sieve was exchanged with 0.6mol / L ammonium nitrate solution three times (1 hour / time), washed with water three times (1 hour / time), dried at 110°C for 5 hours, and then roasted at 540°C for 3 hours with an equal volume of Catalyst Cat-D was prepared by impregnation method with zinc metal loaded at 6.0wt%, dried at 95°C for 8 hours, and calcined at 480°C for 7 hours. Wherein ammonium nitrate exchange and washing temperature is 75 ℃. Gained catalyst detects through XRF, and the Na in this catalyst 2 O is less than 0.05 wt%.
Embodiment 3
[0030] Put 20g of Na-type ZSM-11 molecular sieve in 100ml of a mixed solution of sodium hydroxide with a concentration of 0.6mol / L and TBAOH with a concentration of 0.4mol / L, heat it in a water bath at 70°C for 2 hours, filter and wash to medium Drying at 110°C for 4 hours, calcination at 550°C for 6 hours. The prepared molecular sieves were exchanged with 0.9mol / L ammonium nitrate solution three times (1 hour / time), washed with water three times (1 hour / time), dried at 120°C for 3 hours, roasted at 500°C for 6 hours, and then used an equal volume Catalyst Cat-E was prepared by impregnation method with zinc metal loaded at 7.0wt%, dried at 95°C for 11 hours, and calcined at 550°C for 7 hours. Wherein ammonium nitrate exchange and washing temperature is 80 ℃. Gained catalyst detects through XRF, and the Na in this catalyst 2 O is less than 0.05 wt%.
PUM
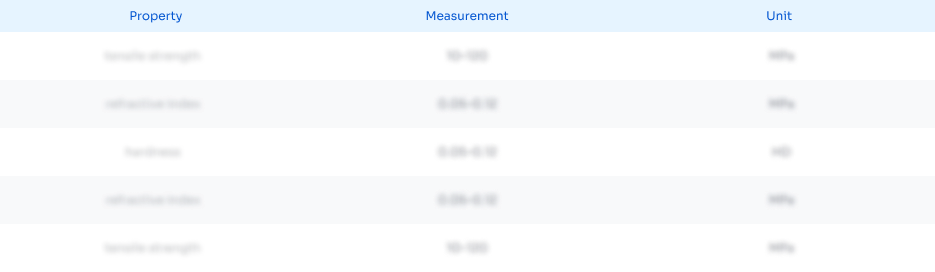
Abstract
Description
Claims
Application Information

- R&D Engineer
- R&D Manager
- IP Professional
- Industry Leading Data Capabilities
- Powerful AI technology
- Patent DNA Extraction
Browse by: Latest US Patents, China's latest patents, Technical Efficacy Thesaurus, Application Domain, Technology Topic, Popular Technical Reports.
© 2024 PatSnap. All rights reserved.Legal|Privacy policy|Modern Slavery Act Transparency Statement|Sitemap|About US| Contact US: help@patsnap.com