Nitrile rubber/polyvinyl chloride composite material and preparation method thereof
A technology of polyvinyl chloride and nitrile rubber, applied in the field of nitrile rubber/polyvinyl chloride composite materials and its preparation, to achieve the effects of improving wear resistance, stability and good hardness
- Summary
- Abstract
- Description
- Claims
- Application Information
AI Technical Summary
Problems solved by technology
Method used
Image
Examples
preparation example Construction
[0020] The embodiment of the present invention discloses a preparation method of nitrile rubber / polyvinyl chloride composite material, comprising the following steps: step a) mixing 70-80 parts by weight of ultra-high nitrile nitrile rubber, 20-30 parts by weight of medium-high nitrile nitrile Rubber and 35-50 parts by weight of polyvinyl chloride are put into an internal mixer, heated to 80-90°C, masticated for 10-30 minutes; step b) is heated to 110-130°C, and 5-10 parts by weight of porous ceramics, 10 -15 parts by weight of nano-boron nitride, 10-15 parts by weight of nano-silicon nitride, 20-30 parts by weight of sprayed carbon black, 4-8 parts by weight of zinc oxide, 2-4 parts by weight of stearic acid, 1-2 parts by weight Zinc stearate, 5-10 parts by weight of plasticizer DOP, 2-5 parts by weight of anti-aging agent RD and 2-5 parts by weight of anti-aging agent MB, kneading for 10-30 minutes, cooling after discharging, to obtain a mixed rubber; Step c) Put the mixed r...
Embodiment 1
[0038] In the polyvinyl chloride emulsion, the radiation crosslinking aid TMPTA is added according to 3-8% of the weight of the dry glue, and then the radiation crosslinking is carried out. After the radiation crosslinking, the polyvinyl chloride emulsion contains ultrafine vulcanized polyvinyl chloride Particles are then spray-dried to obtain ultra-fine vulcanized powder polyvinyl chloride.
[0039] The nitrile rubber / polyvinyl chloride composite material was prepared, and the raw materials and their parts by weight are shown in Table 1.
[0040] Table 1 Preparation raw materials and parts by weight of high-performance nitrile rubber / polyvinyl chloride composites
[0041]
[0042]
Embodiment 2
[0044] A preparation method of a high-performance nitrile rubber / polyvinyl chloride composite material. The material is prepared from the following raw materials in parts by weight: 70 parts of ultra-high nitrile nitrile rubber, 30 parts of medium-high nitrile nitrile rubber, and 35 parts of polyvinyl chloride , 5 parts of porous ceramics, 10 parts of nano boron nitride, 10 parts of nano silicon nitride, 30 parts of spray carbon black, 8 parts of zinc oxide, 4 parts of stearic acid, 1 part of zinc stearate, 5 parts of plasticizer DOP , 0.7 parts of thiocyanic acid, 10 parts of superfine fully vulcanized powder polyvinyl chloride, 0.5 parts of accelerator TMTD, 1 part of accelerator DM, 2 parts of anti-aging agent RD, and 2 parts of anti-aging agent MB.
[0045] The preparation method of described high-performance nitrile rubber / polyvinyl chloride composite material is as follows:
[0046] 1) Put ultra-high nitrile nitrile rubber, medium-high nitrile nitrile rubber and polyviny...
PUM
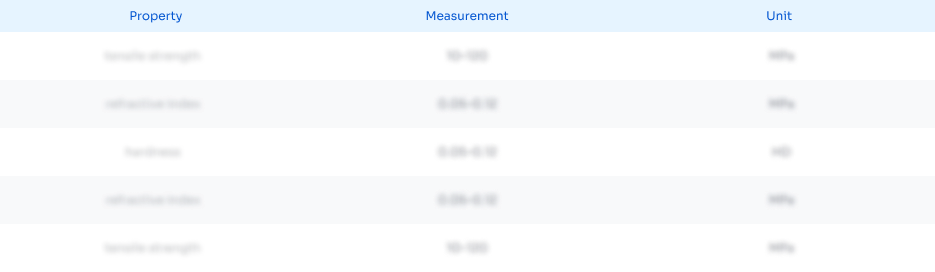
Abstract
Description
Claims
Application Information

- Generate Ideas
- Intellectual Property
- Life Sciences
- Materials
- Tech Scout
- Unparalleled Data Quality
- Higher Quality Content
- 60% Fewer Hallucinations
Browse by: Latest US Patents, China's latest patents, Technical Efficacy Thesaurus, Application Domain, Technology Topic, Popular Technical Reports.
© 2025 PatSnap. All rights reserved.Legal|Privacy policy|Modern Slavery Act Transparency Statement|Sitemap|About US| Contact US: help@patsnap.com