Method for preparing phenyl glycidyl ether
A technology of phenyl glycidyl ether and synthesis method, which is applied in the direction of organic chemistry, can solve the problems of low utilization rate of synthesis method, use of volatile solvents, large environmental pollution, etc., achieve small color number, reduce color number, and product yield high rate effect
- Summary
- Abstract
- Description
- Claims
- Application Information
AI Technical Summary
Problems solved by technology
Method used
Examples
Embodiment 1
[0019] Under nitrogen protection, the stirrer was turned on, and 120 parts of phenol, 2.4 parts of N,N-dimethylethanolamine, 14.4 parts of tetrabutylammonium hydrogen sulfate, and 2.4 parts of polyquaternium-7 were added to the reaction kettle. Heat up, when the temperature reaches 75°C, add 360 parts of epichlorohydrin dropwise, control the temperature at 80-85°C, after 3 hours of dripping, continue to keep warm for 1h; cool down to 50°C, under the protection of nitrogen, at 55-60°C Add 150 parts of 48% liquid caustic soda dropwise at a temperature of 1 hour, and continue to keep warm at a temperature of 55-60 °C for 3 hours; let it stand, drain the salt water, and then wash with 50 parts of soft water, and the lower oil phase is recovered by vacuum distillation. After epichlorohydrin was added, 190 parts of phenyl glycidyl ether were obtained, with a main content of 98.30%, an epoxy value of 0.655 mol / 100 parts, and an APHA color number of No. 10.
Embodiment 2
[0021] Under nitrogen protection, the stirrer was turned on, and 120 parts of phenol, 14.4 parts of N,N-dimethylethanolamine, 4.8 parts of tetrabutylammonium hydrogen sulfate, and 4.3 parts of polyquaternium-7 were added to the reaction kettle. Heat up, when the temperature reaches 75°C, add 360 parts of epichlorohydrin dropwise, control the temperature at 80-85°C, after 3 hours of dripping, continue to keep warm for 1h; cool down to 50°C, under the protection of nitrogen, at 55-60°C Add 150 parts of 48% liquid caustic soda dropwise at a temperature of 1 hour, and continue to keep warm at a temperature of 55-60 °C for 3 hours; let it stand, drain the salt water, and then wash with 50 parts of soft water, and the lower oil phase is recovered by vacuum distillation. After epichlorohydrin was added, 190 parts of phenyl glycidyl ether were obtained, with a main content of 97.61%, an epoxy value of 0.650 mol / 100 parts, and an APHA color number of No. 10.
Embodiment 3
[0023] Under nitrogen protection, the stirrer was turned on, and 120 parts of phenol, 7.2 parts of N,N-dimethylethanolamine, 7.2 parts of tetrabutylammonium hydrogen sulfate, and 2.5 parts of polyquaternium-7 were added to the reaction kettle. Heat up, when the temperature reaches 75°C, add 240 parts of epichlorohydrin dropwise, control the temperature at 80-85°C, after 3 hours of dripping, continue to keep warm for 1h; cool down to 50°C, under the protection of nitrogen, at 55-60°C Add 150 parts of 48% liquid caustic soda dropwise at a temperature of 1 hour, and continue to keep warm at a temperature of 55-60 °C for 3 hours; let it stand, drain the salt water, and then wash with 50 parts of soft water, and the lower oil phase is recovered by vacuum distillation. After epichlorohydrin was added, 190 parts of phenyl glycidyl ether were obtained, the main content was 98.4%, the epoxy value was 0.656mol / 100 parts, and the color number was No. 10.
PUM
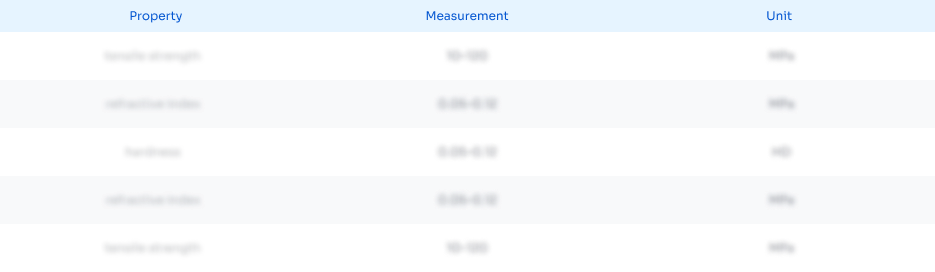
Abstract
Description
Claims
Application Information

- R&D
- Intellectual Property
- Life Sciences
- Materials
- Tech Scout
- Unparalleled Data Quality
- Higher Quality Content
- 60% Fewer Hallucinations
Browse by: Latest US Patents, China's latest patents, Technical Efficacy Thesaurus, Application Domain, Technology Topic, Popular Technical Reports.
© 2025 PatSnap. All rights reserved.Legal|Privacy policy|Modern Slavery Act Transparency Statement|Sitemap|About US| Contact US: help@patsnap.com