A kind of preparation technology of high-strength copper alloy plate
A preparation process and technology for copper alloy plates, applied in the field of copper-based alloy manufacturing, can solve the problems of unsatisfactory processing properties and mechanical properties of copper plates, complex components, and inability to effectively remove harmful copper impurities, etc., so as to improve machining performance, improve Morphology, effect of changing microstructure
- Summary
- Abstract
- Description
- Claims
- Application Information
AI Technical Summary
Problems solved by technology
Method used
Examples
Embodiment 1
[0022] The designed high-strength copper alloy plate is characterized in that the weight percentage of the alloy chemical composition is:
[0023] Al 2%, Sn 3%, Mg 0.10%, Mn 0.01%, Co 0.7%, Fe 0.10%, Ti 0.01%, Ag0.02%, Ta 0.01%, Y 0.01%, the balance is copper and unavoidable non-metallic inclusions.
[0024] The preparation process adopted is as follows: (1) The materials prepared according to the composition of the alloy elements are melted in the melting furnace, and the temperature in the melting furnace is set at 1170-1180 °C, and the obtained molten material is stirred, slag-cleaned, and adjusted for sampling and testing Composition, after the composition meets the formula requirements, it is transferred into the constant temperature furnace, and the temperature of the melt in the constant temperature furnace is 1175°C. (2) The horizontal continuous casting adopts the pull-stop-reverse process, the continuous casting speed is controlled at 180mm / min, and the thickness of...
Embodiment 2
[0026] The designed high-strength copper alloy plate is characterized in that the weight percentage of the alloy chemical composition is:
[0027] Al 3%, Sn 4%, Mg 1.00%, Mn 0.03%, Co 1%, Fe 0.80%, Ti 0.02%, Ag0.04%, Ta 0.02%, Y 0.02%, the balance is copper and unavoidable non- Metal inclusions.
[0028] The preparation process adopted is as follows: (1) The materials prepared according to the composition of the alloy elements are melted in the melting furnace, and the temperature in the melting furnace is set at 1170-1180 °C, and the obtained molten material is stirred, slag-cleaned, and adjusted for sampling and testing Composition, after the composition meets the formula requirements, it is transferred into the constant temperature furnace, and the temperature of the melt in the constant temperature furnace is 1175°C. (2) The horizontal continuous casting adopts the pull-stop-reverse process, the continuous casting speed is controlled at 180mm / min, and the thickness of the...
Embodiment 3
[0030] The designed high-strength copper alloy plate is characterized in that the weight percentage of the alloy chemical composition is:
[0031] Al 2.5%, Sn 4%, Mg 1.00%, Mn 0.03%, Co 1%, Fe 0.80%, Ti 0.02%, Ag0.04%, Ta 0.02%, Y 0.02%, the balance is copper and unavoidable non- Metal inclusions.
[0032] The preparation process adopted is as follows: (1) The materials prepared according to the composition of the alloy elements are melted in the melting furnace, and the temperature in the melting furnace is set at 1170-1180 °C, and the obtained molten material is stirred, slag-cleaned, and adjusted for sampling and testing Composition, after the composition meets the formula requirements, it is transferred into the constant temperature furnace, and the temperature of the melt in the constant temperature furnace is 1175°C. (2) The horizontal continuous casting adopts the pull-stop-reverse process, the continuous casting speed is controlled at 180mm / min, and the thickness of t...
PUM
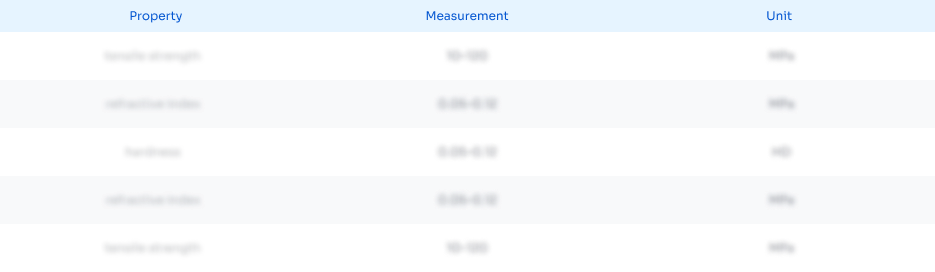
Abstract
Description
Claims
Application Information

- R&D
- Intellectual Property
- Life Sciences
- Materials
- Tech Scout
- Unparalleled Data Quality
- Higher Quality Content
- 60% Fewer Hallucinations
Browse by: Latest US Patents, China's latest patents, Technical Efficacy Thesaurus, Application Domain, Technology Topic, Popular Technical Reports.
© 2025 PatSnap. All rights reserved.Legal|Privacy policy|Modern Slavery Act Transparency Statement|Sitemap|About US| Contact US: help@patsnap.com