Method for treating selenium/mercury-containing acid mud
A treatment method and technology of acid mud, which is applied in the field of metallurgy, can solve the problems of low recycling rate of valuable metals, environmental pollution, etc., and achieve the effects of less investment in equipment, good economic benefits, and simple processes
- Summary
- Abstract
- Description
- Claims
- Application Information
AI Technical Summary
Problems solved by technology
Method used
Image
Examples
Embodiment 1
[0038] ①Take 50g of selenium-containing mercuric acid mud, and analyze the main chemical components: Se 32.85%, Hg 35.44%, Pb 15.12%. Add acid mud to 500ml 300g / L sodium chloride solution, add hydrochloric acid to adjust pH to 1, react at 90°C for 2 hours; add sodium hydroxide to the filtered filtrate to adjust pH to 8, react for 2 hours, lead residue contains Pb 79.85%, Lead sinking slag tempering lead smelting system to recover lead.
[0039] ② Add lead leaching slag to 80g / L HCl solution, under the condition of liquid-solid ratio 10:1, 80℃, add 16.82g sodium chlorate, react for 2h, leaching slag contains Se 3.03%, Hg 0.64%, leaching slag Return to oxidation leaching for secondary leaching; add 40% NaOH to the leachate to adjust the pH of the solution to 13.5, and react for 2 hours to obtain mercury-rich slag with a mercury content of 90.74%; add mercury-rich slag to hydrazine hydrate solution for reduction, and after reduction, the slag is distilled at 240°C 2h, get metall...
Embodiment 2
[0043] ① Take 100g of selenium-containing mercuric acid mud, and analyze the main components: Se 32.85%, Hg 35.44%, Pb 15.12%. Add the acid mud into 1500ml 350g / L calcium chloride solution, add acid to adjust the pH to 1.5, react at 90°C for 2 hours; add calcium oxide to the filtered filtrate to adjust the pH to 8.5, and react for 3 hours. The lead residue contains 81.63% Pb. The lead smelting system of lead slag tempering method recovers lead.
[0044] ② Add lead leaching slag to 100g / L HCl solution, under the condition of liquid-solid ratio 8:1, 60℃, add 100ml hydrogen peroxide, react for 3h, leaching slag contains Se2.73%, Hg 0.41%, leaching slag returns to oxidation Leach for secondary leaching; add 30% NaOH to the leachate to adjust the pH of the solution to 13.0, and react for 2 hours to obtain mercury-rich residue with a mercury content of 86.32%. The mercury-rich residue is reduced by adding hydrazine hydrate solution, and the reduced residue is distilled at 200°C for ...
Embodiment 3
[0048] ① Take 50g of selenium-containing mercuric acid mud, and analyze the main components: Se26.44%, Hg 26.68%, Pb 24.61%. Add acid mud to 600ml 280g / L sodium chloride solution, add acid to adjust pH to 1, react for 2 hours at 85°C; after filtering, add sodium hydroxide to the filtrate to adjust pH to 8, react for 2 hours, lead residue contains Pb80.23% , the heavy lead slag tempering lead smelting system to recover lead.
[0049] ② Add lead leaching slag to 100g / L HCl solution, under the condition of liquid-solid ratio 10:1, 70℃, add 50ml hydrogen peroxide, react for 2h, leaching slag contains Se 2.44%, Hg 0.27%, leaching slag returns to oxidation leaching Perform secondary leaching; add 40% NaOH to the leachate to adjust the pH of the solution to 14, and react for 2 hours to obtain mercury-rich residue with a mercury content of 89.13%; add mercury-rich residue to hydrazine hydrate solution for reduction, and after reduction, the residue is distilled at 240°C for 2 hours to...
PUM
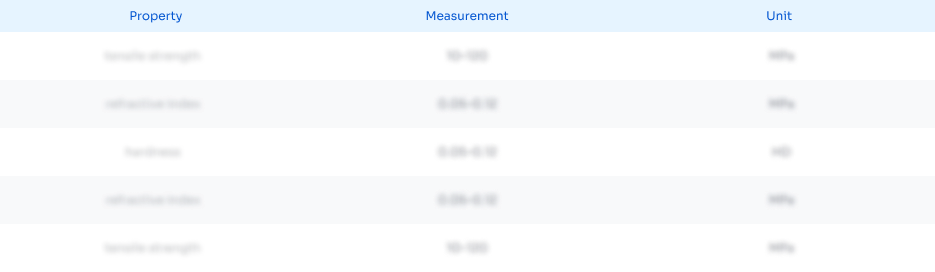
Abstract
Description
Claims
Application Information

- Generate Ideas
- Intellectual Property
- Life Sciences
- Materials
- Tech Scout
- Unparalleled Data Quality
- Higher Quality Content
- 60% Fewer Hallucinations
Browse by: Latest US Patents, China's latest patents, Technical Efficacy Thesaurus, Application Domain, Technology Topic, Popular Technical Reports.
© 2025 PatSnap. All rights reserved.Legal|Privacy policy|Modern Slavery Act Transparency Statement|Sitemap|About US| Contact US: help@patsnap.com