Thermo-oxidative-aging-resistant polypropylene composite and preparation method thereof
A polypropylene and thermo-oxidative resistance technology is applied in the field of thermo-oxidative aging-resistant polypropylene composites and their preparation, and can solve the problems of poor thermo-oxidative aging resistance, large steric hindrance of phenolic hydroxyl groups, and decreased thermo-oxidative aging performance, etc. Achieving good thermal oxidation resistance, low cost and improved efficiency
- Summary
- Abstract
- Description
- Claims
- Application Information
AI Technical Summary
Problems solved by technology
Method used
Image
Examples
Embodiment 1
[0026] 99.2 kg of polypropylene PP (S700), 0.2 kg of hindered phenol heat stabilizer 1010, 0.1 kg of semi-hindered phenol antioxidant AO-80, 0.3 kg of phosphite heat stabilizer 168, and 0.2 kg of processing aid EBS in the long Melt, mix and disperse in a twin-screw extruder with a diameter ratio of 40:1, extrude and granulate at 200°C, and finally obtain a polypropylene compound. Its performance test parameters are shown in Table 1.
Embodiment 2
[0028] 83.9 kg of polypropylene PP (Z30S), 10 kg of talcum powder (3000 mesh), 5 kg of ethylene octene copolymer POE DF610, 0.25 kg of hindered phenol antioxidant 3114, 0.15 kg of semi-hindered phenol antioxidant 1790, 0.4 Kg of phosphite heat stabilizer PEP-36 and 0.3 kg of processing aid calcium stearate were melted, mixed and dispersed in a twin-screw extruder with a length-to-diameter ratio of 40:1, extruded and granulated at 200°C, and finally obtained poly Propylene compound. Its performance test parameters are shown in Table 1.
Embodiment 3
[0030] 73.5 kg of polypropylene PP (BX3800), 15 kg of talcum powder (3000 mesh), 10 kg of ethylene octene copolymer POE 8137, 0.3 kg of hindered phenol heat stabilizer 1076, 0.2 kg of semi-hindered phenol antioxidant 245, 0.5 kg Thioester heat stabilizer 412S and 0.5 kg of processing aid zinc stearate were melt mixed and dispersed in a twin-screw extruder with a length-to-diameter ratio of 40:1, extruded and granulated at 200°C, and finally obtained a polypropylene compound . Its performance test parameters are shown in Table 1.
PUM
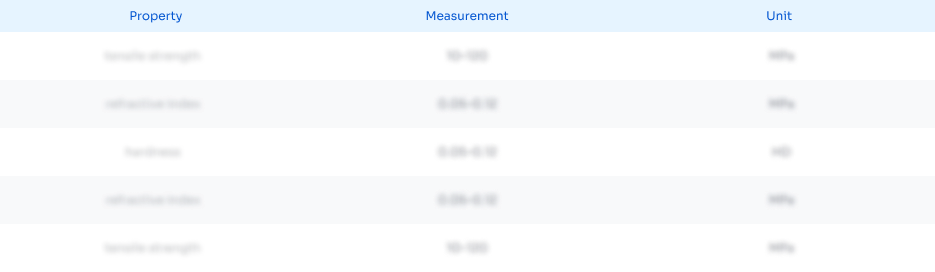
Abstract
Description
Claims
Application Information

- Generate Ideas
- Intellectual Property
- Life Sciences
- Materials
- Tech Scout
- Unparalleled Data Quality
- Higher Quality Content
- 60% Fewer Hallucinations
Browse by: Latest US Patents, China's latest patents, Technical Efficacy Thesaurus, Application Domain, Technology Topic, Popular Technical Reports.
© 2025 PatSnap. All rights reserved.Legal|Privacy policy|Modern Slavery Act Transparency Statement|Sitemap|About US| Contact US: help@patsnap.com